C3's Top 5 Must-Reads on Dock Appointment Scheduling
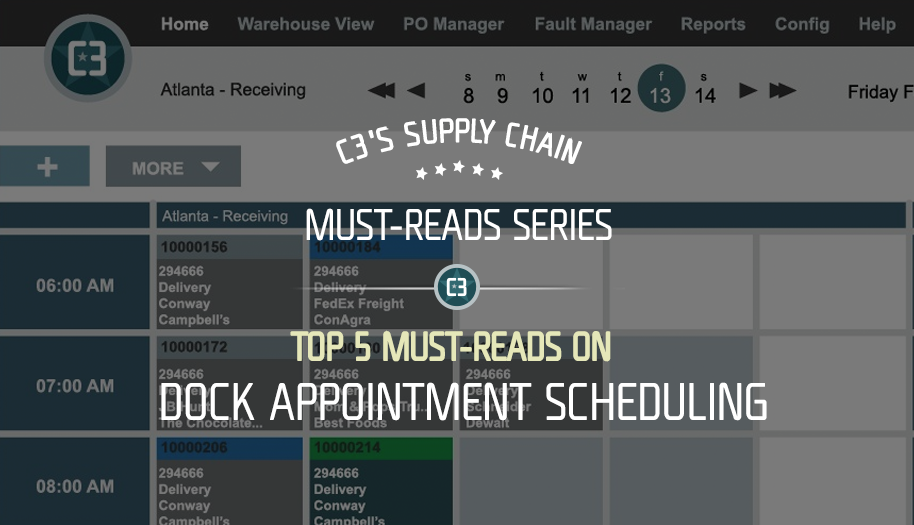
Welcome to C3 Solutions' Top Must-Reads series - Volume 5.
This is the fifth of a 7 blogs series featuring C3's selection of of the top must-reads on various supply chain and logistics hot topics: Cloud Supply Chain Systems, The Internet of Things, Chain of Responsibility, Becoming a Shipper of Choice, Technology Reshaping the Modern Supply Chain, Yard Management & Dock Scheduling systems and best practices.
Our last Top Must-Reads (Volume 4) covered our most popular resources and blog posts on Becoming a Shipper of Choice.
For this Top Must-Reads Volume 5, we have gathered our most popular resources and blog posts related to dock appointment scheduling.
Here's C3's Top 5 Must-Reads on Dock Appointment Scheduling
1 - Understanding Dock Scheduling - WHITE PAPER
This white paper's objective is to help industry professionals understand the basics of dock scheduling, supported by real industry case studies. It will help you:
- Assess whether you need a dock scheduling system
- Identify your potential cost savings
- Determine where to start
- Evaluate which solution is best for your business
You will also find a comparative table for an easy comparison between different types of dock scheduling systems versus their criteria and benefits.
2 - The Underestimated Value of Dock Scheduling - WHITE PAPER
How much are reports and dashboards worth to your organization?
- How can you measure your scheduler’s efficiency?
- How can you audit chargebacks and demurrage fees?
- What is measurable and how is it useful?
- Who, in your organization, could benefit from reports and dashboards?
These are all questions addressed in C3 Solutions’ white paper ‘The Underestimated Value of Dock Scheduling‘.
3 - 3 Essentials to Overcome your Dock Scheduling Madness
Docks, be they traditional warehouses, manufacturing sites, retail stores, hospitals or convention centers, can be very complicated to manage. At a high level, it’s simply about getting product in and out of the warehouse and turning drivers around as quickly as possible. However, the shear relative volumes and the numerous variables in play can quickly turn your dock operations into a complicated logistics operation. What are the symptoms that something is amiss in your dock operations? Can you identify the direct costs associated? What possible solutions exist?
4 - 3 Key Tips to Improve your Dock Scheduling Operations
You may consider that your business has a ‘’scheduling process’’, yet the fact that appointment requests, confirmations, amendments and cancellations are executed via emails and phone calls is totally inefficient. In fact, within the realm of dock scheduling, inefficient communication is the most expensive facet of the operation. Here are 3 Key Tips that could definitely change the face of your dock scheduling operations.
5 - 10 Signs you've Outgrown your Dock Scheduling Process
Most warehouse operations invest very little time and money in their dock scheduling solutions, and quite frankly in the past there were not a lot of options out there.
The costs of not managing your dock properly are high, both from an opportunity and monetary perspective. Are you able to get more throughput from your dock with the same work force? Will you be able to respond to the pressure from your carriers to become more “carrier friendly”? More importantly what is that tipping point that makes taking action a no-brainer?