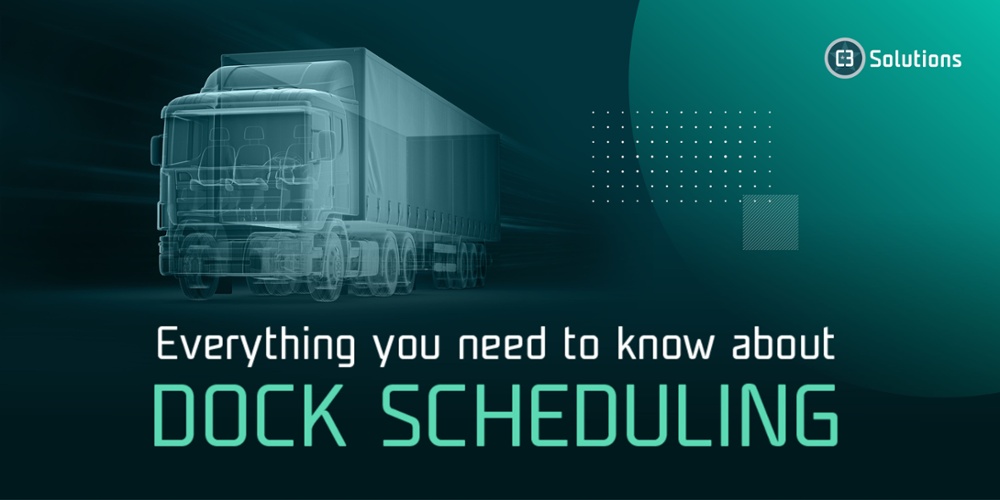
4. What’s a Dock Scheduling Software?
A dock scheduling software is a digital tool designed specifically to tackle the challenges we’ve discussed. It’s sometimes also called a dock appointment scheduling system or an appointment management system for warehouses. Whatever the name, the concept is the same: this software provides a centralized platform to schedule and manage all the dock appointments at your facility (or across multiple facilities).
Think of dock scheduling software as a smart, shared calendar on steroids – one that understands the ins and outs of your operations. Instead of a static spreadsheet or calendar, it allows for dynamic scheduling with rules and real-time updates. Warehouse managers use it to set the parameters (available dock doors, operating hours, types of loads each door can handle, etc.), and carriers or vendors can see available time slots and book appointments through a web portal. The system will enforce your business rules automatically – for example, preventing double-booking of a dock, or blocking scheduling of certain load types back-to-back if you require a buffer time.
A best-in-class dock scheduling system does more than just list appointment times. It typically will:
- Optimize scheduling based on capacity: It helps plan and level-load the work. For instance, it can factor in how many trucks you can unload at once, or how long certain types of appointments take, to avoid overloading your team.
- Provide self-service access: Carriers, suppliers, or drivers can log into an online portal 24/7 to request or book their own appointments within the rules you’ve set. This drastically cuts down on the back-and-forth communications.
- Automate confirmations and notifications: Once an appointment is booked or changed, the software sends automatic email confirmations to relevant parties (and can even integrate to send texts or other alerts). No more “Did you get my email?” phone calls – everyone is on the same page instantly.
- Maintain a live schedule: All users see the real-time status of the dock schedule. If a truck is delayed or a slot opens up, the system can update and even notify interested parties. This live visibility is worlds better than a printed spreadsheet that’s outdated the moment it’s printed.
- Record data and timestamps: As appointments are fulfilled, the software can log arrivals, departures, and unloading durations. Many systems let the dock crew check in trucks (e.g. via a kiosk or a mobile app) and mark when they begin and finish at the dock. This builds a wealth of data for analysis, which manual systems lack.
- Integrate with other systems: A good dock scheduling software isn’t a standalone island (more on this later). It can pull in relevant data like purchase order numbers or load IDs from your other systems, and in turn push out schedule updates to those systems. This ensures that, for example, your transportation management system knows the appointment time a carrier picked, or your warehouse management system is aware a delivery has been scheduled.
Dock scheduling software is the purpose-built solution to coordinate the who, when, and where of loading docks. Instead of juggling emails or relying on someone’s memory, you have an organized system that makes scheduling faster, more transparent, and more accurate. By handling the heavy lifting of appointment management, the software frees up your staff’s time and reduces human error – all while providing a better experience for carriers and suppliers who interact with your facility.
5. How a Dock Scheduling Software Works
Understanding how dock scheduling software works will give you a clearer picture of its value. While each system has its own interface and features, the general workflow is usually as follows:
-
Setup of Schedules and Rules:
The warehouse or DC defines its scheduling parameters in the software. This includes the number of dock doors and their operating hours, the types of appointments (inbound vs outbound, full truckload vs LTL, etc.), and any business rules or constraints. For example, you might configure that a particular dock door only handles refrigerated loads, or that no more than 2 heavy loads are scheduled in the same hour. You can also preload standing appointments (for regular daily/weekly deliveries) and set blackout times (e.g. lunch breaks or shift changes) when no appointments should be booked.
-
Carrier Self-Service Portal:
Carriers, vendors, or drivers are given access (usually via a secure web portal login) to book appointments. When a carrier needs to deliver or pick up, instead of calling or emailing, they enter the portal and see a calendar of available slots that meet the criteria (for instance, they select the facility and load type, and the system shows open times that fit). They can then choose an open slot that works for them and reserve it. The system might require them to input relevant info like trailer type, load ID or purchase order number – ensuring all details are captured upfront. Once they submit, the appointment is booked instantly.
-
Automated Confirmation and Updates:
The moment an appointment is booked (or changed), the dock scheduling software sends out confirmations. An email notification might go to the carrier with the confirmed date/time and a reference number, and notifications can go to warehouse staff as well. This replaces the manual step of someone emailing “Your appointment is confirmed for 10 AM” – it’s all automatic. If the carrier needs to reschedule, they can adjust it in the portal (within the allowed rules), and everyone gets updated notifications. The system maintains a single live schedule that all parties refer to, eliminating confusion. No more “version control” issues like two people updating different spreadsheets; the portal is the single source of truth.
-
Day-of-Arrival Management:
On the day of the appointment, many systems provide tools to manage the flow. For example, when a truck is en route, the carrier might check it in via a mobile app or a geo-fence might update the ETA. Some advanced setups have electronic gate check-in where a guard or kiosk logs the truck’s arrival into the system. The dock staff can see which truck has arrived and for what appointment. The software can assign a dock door if not already assigned, or even dynamically adjust dock assignments if unexpected delays or opportunities arise (some AI-driven systems now do this automatically to reduce congestionv). Warehouse workers might receive a notification on a handheld device that “Truck #123 for PO 456789 has arrived at Gate” so they can prepare to unload.
-
Processing and Turnaround Tracking:
As loading or unloading happens, the system can track key timestamps. Many warehouses integrate mobile devices or barcode scans into this process. For example, in one case a company set up a process where, once an order was staged and ready to ship, the shipping lead scanned a barcode on the system-generated appointment sheet to mark it “Ready for pickup,” and later scanned again when the truck was loaded and departed. All these events (arrival time, “on dock” time, completion time, etc.) can be captured. Even without fancy scanning, staff can manually update status in the software (e.g., mark “Arrived” or “Completed”). The result is you know exactly when each truck arrived at the facility, when it got on the dock, and when it left.
-
After-Action Data and Visibility:
The dock scheduling software maintains a history of all appointments and their outcomes. Managers can pull reports or even real-time dashboards: for example, viewing the day’s schedule across all docks, seeing how many trucks are currently in the yard, or reviewing yesterday’s performance (how many were on-time vs late, average unload duration, etc.). This data is gold for continuous improvement – you might discover, for instance, that a particular carrier is always late on Mondays, or that one type of load consistently takes longer than the assumed time, prompting you to adjust slot durations. Good systems often come with built-in KPIs and audit logs to measure things like carrier performance and dock utilization.
Throughout this process, integration with other systems often plays a role. For example, the software might send a message to your Warehouse Management System when a truck is marked “arrived” so inventory receiving can begin, or send a pickup confirmation to your Transportation Management System once an outbound load is departed. In the ideal scenario, the dock scheduling system “talks” to your WMS, TMS, ERP, and even yard management system, so that everyone – and every system – knows what’s happening in real time.
In summary, dock scheduling software works by digitizing the appointment life cycle from booking to check-out. It creates a streamlined, transparent process that replaces the phone tag, email chains, and guesswork of manual scheduling with an efficient, rules-driven workflow. The end result is a more predictable and manageable operation for you, and a smoother experience for your carriers and customers.
6. Benefits of a Dock Scheduling Software
Implementing a dock scheduling software can yield tremendous benefits for warehouses and distribution centers. We’ve touched on a few already, but let’s break down the major benefits and improvements you can expect:
Reduced Wait Times (and Lower Detention Fees):
One of the most immediate benefits is cutting down truck wait times. When schedules are optimized and communicated, drivers spend far less time sitting in queue. This directly slashes your detention costs (fees paid to carriers for waiting). For example, the food distributor that was once overbooked and drowning in chaos saved more than $35,000 per month in detention charges after deploying a dock scheduling system. With appointments spaced out properly and priorities clear, drivers arrive, dock, and depart with minimal idle time – meaning your company isn’t paying for avoidable delays. It also reduces yard congestion and the risk of bottlenecks.
Higher Dock & Warehouse Productivity:
Smoother scheduling leads to better use of your docks and labor. By leveling the workload and preventing random surges of activity, a scheduling system ensures docks are rarely empty or overwhelmed – they stay efficiently utilized. Warehouse crews can maintain a steady rhythm of work, which is far more productive than the hurry-up-and-wait that often happens with poor scheduling. An organized schedule also makes it easier to handle high volume days. Overall, you can move more trucks through the facility in a given time. Many companies find they can significantly increase throughput without adding docks or staff, simply by eliminating the inefficiencies. Productivity also rises because workers spend less time on administrative tasks (like coordinating arrivals or chasing info) and more on actual loading/unloading. For instance, at the ice cream warehouse, employees recouped about 4-5 hours of work time per week once they ditched the spreadsheet system – time which could be redirected to managing inventory or other value-add activities.
Improved On-Time Performance:
With a solid scheduling process, your operation’s on-time metrics will improve both inbound and outbound. Inbound, that means you’re getting raw materials or products when expected, avoiding stockouts on the production line or shelves. Outbound, it means customer orders leave as promised, bolstering your service level. One case study showed that after implementing dock scheduling across multiple sites, driver wait times vanished and customer complaints about late deliveries disappeared. When trucks are consistently on schedule, it strengthens the entire supply chain’s reliability.
Enhanced Visibility and Communication:
Dock scheduling software provides a single source of truth for appointments. All stakeholders – warehouse teams, transportation planners, carriers, even buyers or customer service reps – can gain appropriate visibility. Many systems allow internal users to view the schedule in real time, or even send tracking links to external parties. This transparency means fewer “Where is my truck?” inquiries because the information is readily available. Internally, departments operate with better coordination: for example, the purchasing team can see when an urgent inbound shipment is due to arrive, or the shipping office knows which orders are being picked for the afternoon truck. Some systems also allow automated alerts; e.g., if a truck hasn’t shown up by its appointment time, it can trigger a notification to management. Overall, communication improves as everyone trusts the system to keep them informed, rather than relying on Bob’s clipboard or Susan’s email thread.
Carrier and Driver Satisfaction (Becoming a Shipper of Choice):
When you make life easier for carriers, you become their preferred customer. Dock scheduling software enables a “self-service” model for carriers that they truly appreciate – no more tedious calls and voicemails, they can manage appointments online on their own schedule. Additionally, when they arrive, they’re not stuck waiting forever because you’ve planned capacity. This kind of efficiency and respect for the driver’s time earns goodwill. In a tight trucking market, that can translate to carriers prioritizing your loads or offering better rates. C3 Solutions notes that effective dock scheduling directly boosts your reputation as a shipper of choice in the eyes of carriers. Carriers know which warehouses are notoriously slow (drivers exchange these stories!); by using a modern scheduling system, you signal that your facility is organized, quick, and driver-friendly. Happier carriers means a more resilient transportation network for you.
Labor Efficiency and Morale:
A predictable schedule is also a boon for your warehouse staff. It allows supervisors to plan shifts with confidence, reducing the need for sudden overtime or frantic calls for extra help. Employees can anticipate busy periods and are less likely to be caught off guard by a convoy of unannounced trailers. In the food distributor case, the manager highlighted that with C3’s system they could ensure having the right labor on hand at the right time for the 115 trucks a day. No more constantly fighting fires – the team can work proactively. This improves morale, as workers prefer a steady, manageable workload over an erratic one. It also improves safety: when the dock is not overfilled and rushed, workers can follow standard operating procedures more closely (and as mentioned, avoid unsafe situations like blocked exits or rushing forklift work).
Data-Driven Insights and Continuous Improvement:
By capturing detailed data on each appointment, dock scheduling software lets you analyze and improve your operations. You can track key performance indicators like average load/unload time per carrier, percentage of on-time arrivals, turnaround time per dock, etc. These insights can highlight chronic issues – maybe one supplier is always late, or one dock door is underutilized, or certain load types consistently take longer than scheduled. With this information, you can take action: maybe extend certain appointment durations, add buffer time for certain suppliers, or provide feedback to carriers who are underperforming. Essentially, the software provides an audit trail and reporting that manual methods lack. Some systems even include scorecard features for carrier performance or dashboards that quantify things like detention time saved, giving you concrete evidence of the efficiency gains. All of this supports a culture of continuous improvement at the dock.
Reduced Errors and Administrative Burden:
Automating the appointment process greatly reduces human error. Typos, double entries, lost emails – those become non-issues when the software handles the info. For example, instead of someone retyping a freight order into a calendar and possibly mistyping it, the carrier might select the exact order number from a drop-down (fed from your system), ensuring accuracy. In one case, a snack food manufacturer using C3 Reservations found that automating their carrier assignments (having the system auto-email load info and track responses) eliminated errors from manual re-entry and saved the transport team a lot of stress. Overall, schedulers and clerical staff are freed from the drudgery of constant email replies and manual record-keeping. This not only saves time but improves accuracy of the schedule data.
Better Emergency Handling:
Even with great planning, things go wrong – a truck breaks down, weather disrupts shipments, etc. Dock scheduling software gives you tools to react more nimbly. You can quickly find the next available slot to reschedule a delayed truck and notify all parties with a few clicks. Or if you suddenly need to receive a critical load ASAP, you can shuffle the calendar (with full visibility of impacts) to squeeze it in, perhaps moving a less urgent appointment slightly later. This flexibility ensures that exceptions can be managed with minimal chaos, maintaining service levels even when the unexpected happens.
Regulatory Compliance and Security:
A less obvious benefit, but important: having a documented schedule and record of all truck movements can help with compliance. For instance, facilities aiming for C-TPAT (Customs-Trade Partnership Against Terrorism) certification need to control and document site access for carriers. One C3 Solutions customer (a consumer goods manufacturer) found that moving from ad-hoc Google Sheets scheduling to a secure dock scheduling system improved its ability to meet C-TPAT security requirements, since the software provided greater visibility and control over who was coming on site and when. Additionally, electronic records of arrivals and departures can support compliance with labor regulations (e.g., proving that drivers did not exceed waiting times) or safety audits. By automating documentation (like time stamps, bill of lading attachments, etc.), the system creates a digital paper trail that can be very useful for audits and regulations.
It’s clear that the benefits of a dock scheduling software touch nearly every aspect of warehouse operations – from hard savings in dollars to softer gains in relationships and employee well-being. The ROI can be remarkable and, in many cases, quickly realized. Many companies report that a SaaS (cloud) dock scheduling solution pays for itself within months through cost savings and efficiency gains. In short, if your facility has any significant volume of truck traffic, implementing a dock scheduling system can dramatically transform your performance and help turn your dock into the well-oiled “front door” of your warehouse that it’s meant to be.
C3 ROI Calculator
Here are some pain points you can quantify in dollars. Open a new spreadsheet and start entering:
While for some of you the need for a scheduling system is painfully obvious, and the pressure to implement one may be coming from senior management, for others it might be necessary at this point to demonstrate the value to management before you can get the budget to proceed. In that case, the next step is to estimate the cost of inefficient operations.
- Driver detention fees
- Unnecessary trailer demurrage fees
- Unscheduled overtime pay
- Premium transportation services
- Lost shipments
- Lost time injury costs due to poor loading dock safety practices
- Fines for breaking health and safety regulations due to trip and fall hazards or improperly maintained equipment
Use our ROI Calculator to calculate your yearly savings and download your free report:
7- Key Features to Look for in Dock Scheduling Software
Not all scheduling tools are created equal. When evaluating dock management software (whether an all-in-one logistics scheduling software or a standalone dock scheduler), it’s important to know the features that truly make a difference. Here are some essential features and capabilities you should expect from the best dock scheduling software solutions:
-
Online Self-Service Portal:
A cornerstone of modern dock scheduling is an online portal where carriers, vendors, or customers can book and manage their appointments. This dock portal (or carrier portal / client portal) should be accessible 24/7 via the web. It allows external parties to see available time slots and reserve or request one that suits them, within rules you define. Self-service greatly reduces emails and calls. For example, instead of your coordinator phoning five carriers to confirm who can pick up a load at 4 PM, you can post that slot and let the first carrier to accept take it. Look for features like slot search, appointment requests/approvals, and the ability for users to upload relevant info (PO numbers, ASN, etc.) during booking. A user-friendly portal turns your dock appointment scheduling software into a collaborative platform rather than just an internal calendar.
-
Automated Notifications & Confirmations:
The system should handle the routine communications automatically. When an appointment is booked or changed, notifications go out to all relevant parties (warehouse staff, the carrier dispatcher, the driver via text, etc.). Reminders should be sent before the appointment (e.g. 24 hours prior) to reduce no-shows. And if a carrier needs to confirm the appointment (common in outbound loads where you assign a pickup time and they must acknowledge it), the system should facilitate that. One case study showed how automating the “carrier confirmation” process – where a carrier simply clicks Accept or Decline on an emailed request – removed a huge burden from the shipper’s transportation team. The software kept track of who hadn’t responded and even sent alerts after 4 hours of no reply, so no load request fell through the cracks. These kinds of automatic alerts and follow-ups ensure nothing gets forgotten.
-
Flexible Time Slot Configuration:
Your scheduling tool should allow different appointment lengths and rules. As mentioned, not every truck is equal – unloading 20 tons of bulk material might take 3 hours while dropping off a small parcel might take 15 minutes. The software should let you set default durations for different load types or allow dynamic calculation based on load details (pallet count, etc.). Being able to configure buffer times between appointments at the same dock, or limits on how many trucks per hour can be handled, is also important. This intelligent slot management prevents overloading your team. It’s even better if the system can integrate with labor standards or equipment capacity (for instance, linking with a Labor Management module to assign time based on how long an unload should take if you have one forklift vs. two). The more the system can optimize slot lengths automatically, the more efficient your schedule will be.
-
Dock and Yard Visibility:
While scheduling is the focus, it really helps if the software provides a visual calendar and real-time status updates. A drag-and-drop calendar view of all docks and appointments is great for dispatchers to get a snapshot of the day. If a truck is checked in at the gate or has docked, having that status update in the system (possibly via integration with a yard management system or gate check-in tool) will let everyone know the truck is “in progress.” Some systems color-code appointments (scheduled, in process, completed, no-show, etc.) for quick reference. This kind of real-time visibility extends to external users too – e.g., a carrier can see if their truck has been marked “unloaded” and is ready to depart, which improves communication. Essentially, the software should function as a live control tower for dock activities, not just a static plan.
-
Integration Capabilities (WMS, TMS, ERP):
The dock scheduling system shouldn’t exist in a silo. Look for tools that can integrate with your other software – especially your WMS, TMS, or ERP. Integration can be as simple as syncing reference data (like PO numbers, order info, carriers, etc.) so that when someone books an appointment, they must enter a valid order number that matches your records. This was actually a real example: an ice cream warehouse integrated their scheduling system with their order management system to ensure every appointment captured the correct order details, freight type, temperature requirements, etc., with no manual re-keying. Integration can also mean sharing schedule info with a YMS so that yard drivers know which trailer to bring to a door next, or updating your TMS when a pickup is completed. Some advanced logistics scheduling platforms come as part of a suite that includes yard management, freight management, etc., making integration seamless. But even standalone, having API or EDI capabilities to talk to your other systems is key – it eliminates duplicate data entry and ensures that everyone, in every system, is working off the same plan.
-
Analytics and Reporting:
We touched on the data benefits earlier – your dock scheduling software should offer reporting dashboards. Common metrics might include average dwell time per carrier, % of on-time vs late arrivals, number of appointments per day (and utilization vs capacity), and no-show rates. It’s also useful to have reports on who is requesting changes frequently, or what times of day are most/least busy (to adjust staffing accordingly). Some systems even provide KPI benchmarks or goal tracking (for example, setting a target that 90% of trucks depart within 30 minutes of loading completion). These insights help you continuously improve and also demonstrate ROI of the system to higher-ups.
-
User Roles and Permissions:
In an enterprise setting, you’ll want to control who can do what. For instance, suppliers might be allowed to request an appointment but not finalize it unless approved by a warehouse coordinator. Or a carrier might be able to directly book in an available slot but only at a specific facility they serve. Internally, you may have admins who configure the system, versus managers who approve exceptions, versus operations staff who just view the schedule. Robust permission settings (and single sign-on support for convenience) are hallmarks of a mature solution.
-
Mobile Access and Ease of Use:
Don’t overlook usability – the software should be easy to navigate for all users and ideally mobile-friendly. Dock supervisors might be walking the floor with a tablet and need to check the schedule or update an appointment status on the fly. Drivers might benefit from mobile check-in or QR code scanning on arrival to expedite the process. For example, one C3 Solutions customer implemented a neat workflow: when an order was staged and ready for pickup, they’d place a printed summary with a barcode in a sleeve on the pallet; the shipping clerk would then scan that barcode with a phone at the dock to mark the appointment as “ready” and later “completed” in the system. This kind of mobile convenience sped up their process and kept digital records up to date without manual data entry. So, look for features like scanning support, driver kiosk or mobile check-in options, and a responsive design that works on various devices.
In summary, the appointment scheduling software features that matter most are those that remove manual effort, increase visibility, and fit your operational needs. If a solution checks these boxes – self-service booking, automation, flexibility, integration, and ease of use – you’re on the right track.
8- Dock Scheduling and Yard Management: The Bigger Picture
Dock scheduling doesn’t exist in isolation. It’s a crucial piece of the broader dock and yard management puzzle. Many companies start by tackling scheduling and then integrate it with a yard management system (YMS) for even greater efficiency. In fact, surveys show only about 25% of warehouses have implemented a YMS, and even fewer (10%) have automated dock scheduling, but those numbers are growing as facilities seek end-to-end visibility from the gate to the bay door.
How do dock scheduling and yard management work together? Think of YMS as the tool that manages all the trailers, yard trucks, and parking spots outside your warehouse, while dock scheduling manages the flow inside at the docks. When combined, a dock and yard management system can seamlessly orchestrate the movement of trailers from yard to dock and vice versa. For example, once a truck appointment is scheduled and the truck checks in at the gate, a YMS can assign it to a yard slot or directly to a door if available. If there’s a wait, the YMS queues trucks in a “virtual line” (sometimes called queue management) and then notifies the driver via SMS or a driver app when their dock is ready. This avoids actual lineups at the gate or dock – trucks can park in a staging area until called, reducing congestion and idling.
Moreover, yard management can help with drop trailer situations – if a trailer is dropped, the YMS will track its location in the yard and you can schedule a dock time for unloading it when labor is available. Without a YMS, dropped trailers might sit forgotten or you rely on clipboard notes to manage them. Together with a scheduling system, you get a complete picture: you know when each trailer is planned at a dock and where it is currently. This tight integration can significantly cut overall dwell time and ensure every minute is productive. In essence, inbound dock management paired with yard management means from the moment a truck enters your facility to the moment it leaves, you have a controlled, efficient flow.
Another aspect of the bigger picture is integrating transportation scheduling software or your TMS. If your dock scheduler knows that Truck XYZ is running late (perhaps via a telematics integration or because the carrier updated the appointment status), that info can feed into your transportation planning – maybe you adjust loading order or send an alert to a customer about a potential delay. Conversely, your TMS might feed the dock schedule with advance shipment info (e.g. telling the dock system that three trucks are inbound tomorrow from a certain consolidation center, so placeholders can be set). The goal of tying these pieces together is a unified logistics operation where freight booking software, cargo tracking, dock scheduling, and yard management all share data. We’re seeing more of this convergence in “smart warehouse” initiatives, where IoT devices (like gate sensors, RFID tags on trailers, etc.) and software work hand-in-hand to automate as much as possible.
The bottom line: when evaluating dock scheduling needs, it’s wise to consider how it will connect to your yard and transportation processes. If you eventually plan to implement a YMS, look for a scheduling solution that either includes yard management or can integrate with one easily. Some vendors offer an integrated dock and yard management system, which can be attractive for simplicity. But even separate systems should talk to each other – for example, via APIs that update when a truck checks in or a dock assignment is made. The payoff is a truly holistic approach to loading dock management: right truck, right dock, right time – with minimal idle yard time and maximum efficiency.
Trends and Future Outlook in Dock Scheduling
Dock scheduling may sound like a niche topic, but it’s becoming a hot area for innovation as warehouses seek any edge to improve efficiency. A few notable trends and what they mean for you:
-
Growth of Cloud-Based Solutions: Gone are the days of clunky on-premise scheduling tools. Modern dock scheduling software is largely cloud-based, meaning easier updates, scalability, and remote access. Cloud systems also make it simpler to extend access to external partners (carriers, suppliers) since they just log into a web portal. This aligns with the general trend of digital transformation in logistics – everything is moving to the cloud for flexibility and real-time collaboration.
-
Real-Time Visibility and IoT Integration: Closely related is the trend towards greater real-time visibility in yard and dock management. IoT devices and sensors – such as GPS on trucks, RFID tags on trailers, or Bluetooth beacons at gates – are being linked with dock scheduling systems to provide live updates. For example, geofenced alerts can tell the dock scheduler when a truck is 15 minutes away, so the system can prompt “prepare Door 2” or even automatically check in the truck. Live tracking data can also feed into real-time dashboards showing the status of all appointments (arrived, in-process, delayed, completed). This not only helps the warehouse react instantly to delays or early arrivals, but also provides transparency to external stakeholders. Some shippers are giving suppliers or customers access to live tracking of their loads through the dock scheduling platform, so they know exactly when to expect unloading or loading completion. The investment in such real-time visibility tools is growing because companies recognize that you can’t react to what you can’t see. Even beyond the dock, end-to-end visibility (from manufacturer to warehouse to final destination) is the holy grail, and dock scheduling data is a critical piece of that puzzle
-
Market Momentum: The dock scheduling software market is on a strong upward trajectory. Businesses of all sizes are recognizing the ROI. In 2024 the global market was estimated around $4.2 billion and it’s projected to more than double to over $10 billion in the coming decade. That’s roughly a 10% annual growth rate. What’s driving this? Simply put, the pressure for operational efficiency and data-driven decision making in logistics. Companies are investing in these tools because the old ways can’t keep up with today’s supply chain demands. If you’re shopping for a solution, this vibrant market means you have lots of vendor options and continuous innovation fueling new features.
-
IoT and Real-Time Data: As mentioned, integration of IoT devices is a game changer. Think electronic dock sensors that detect when a trailer is in place or when a bay door opens/closes – feeding that status into your software automatically. Or GPS on trucks giving live ETA updates to the schedule. Some warehouses use driver check-in kiosks or geofencing that alerts the system when a truck is near. All this real-time data helps make scheduling systems more dynamic and precise. We’re not far from an era where an arriving truck might automatically trigger a notification to the next one in line, like “your door will be ready in 15 minutes,” based on live unloading progress.
-
AI and Predictive Scheduling: Artificial intelligence is buzzing everywhere, and dock management is no exception. Vendors are starting to offer AI-enhanced features like predictive slot booking – e.g., the system might analyze historical data and current conditions to suggest the optimal schedule for incoming trucks to minimize wait and total operation time. Machine learning could help forecast delays (if a certain carrier is usually late for afternoon slots, the system can proactively adjust their future appointments or pad the schedule). AI might also assist in automatically resolving conflicts or suggesting re-allocations if something changes last-minute. We can expect automated scheduling for warehouse and delivery operations to only get smarter. In the near future, a lot of the schedule tweaking that humans do today could be handled by algorithms that continuously learn from your warehouse’s patterns.
-
Focus on User Experience: As new generations of workers enter the industry, there’s a push for more modern, user-friendly interfaces. The old green-screen or ultra-technical systems are being replaced by apps with intuitive dashboards, drag-and-drop calendars, and even mobile apps. The easier the system is to use, the more broadly it gets adopted – which is crucial for appointment scheduling where you might have hundreds of external users. Expect to see continued improvement in UI/UX, including support for multiple languages (useful if your carriers’ dispatchers are global) and accessibility from any device.
All these trends point to one thing: adopting dock scheduling technology is not just a one-time fix, but a step into a continuously improving ecosystem. Early adopters are already enjoying benefits, and those who haven’t started yet have ever better options to choose from. It’s fair to say that in the future, automated dock scheduling will be as common and essential as having a WMS – it’s becoming a standard best practice for efficient warehouse and transport scheduling operations.
9- Choosing the Right Dock Scheduling System
If you’ve decided it’s time to implement dock scheduling software, the next big question is: How do you choose the right one for your operation? There are many options on the market, from simple add-ons to full-fledged enterprise systems. Plus, you might be weighing building your own vs buying a solution. Below, we break down key considerations to help guide your decision.
Key Features and Functionality to Look For:
At minimum, the system should cover the basics of scheduling, but to future-proof your choice, consider these functional criteria (based on industry best practices and C3’s own guide):
- Carrier/Supplier Portal: A web portal for carriers and suppliers is a must-have. This external-facing component is what enables self-service booking and updates. Make sure the portal is secure, easy to use, and accessible 24/7 (so carriers in any time zone can self-serve). It should also allow external users to view their upcoming appointments and edit or cancel if needed (within the rules). A bonus is if the portal supports multiple languages and time zones – helpful if you deal with international partners.
- Multi-Site Support: If your company has more than one warehouse or DC, the software should handle multiple sites easily – ideally all from one interface. You should be able to manage schedules at different locations independently, while consolidating data for a big-picture view.
- Standing Appointments: The ability to set up recurring appointments (standing time slots for regular daily/weekly deliveries) is crucial. This saves time for repetitive schedules and ensures long-term partners have their reserved slots, while still allowing flexibility to adjust as needed.
- Flexible Booking Rules & Constraints: Look for a highly configurable rules engine. The system should let you enforce your unique constraints – whether it’s limiting a certain type of load per day (like the rug or container examples), or setting cut-off times (e.g. no bookings less than 24 hours in advance), or differentiating by load type, carrier, priority, etc. A one-size-fits-all approach won’t work; the software must adapt to your operational logic.
- Variable Appointment Durations: Not all appointments are equal – unloading 26 pallets of one product might take 30 minutes, while unloading 1,000 loose boxes might take 3 hours. Your dock scheduling tool should allow custom appointment lengths and automatically calculate duration based on data (for instance, pallet count or load size). This ensures the schedule reflects reality, with longer slots for bigger jobs and shorter ones for quick moves.
- Document Handling: Consider systems that let you attach or link documents to appointments. For example, attaching advance shipping notices, packing lists, purchase orders, or Bills of Lading to the appointment record can be very useful. It makes all relevant info accessible in one place for the receiving/shipping clerks.
- Automated Notifications: The system should automatically send email or SMS notifications for key events. For instance, when an appointment is booked, when it’s approaching (“Reminder: you have a delivery at 10 AM tomorrow”), when a load is marked as no-show or running late, etc. Ideally, these triggers are configurable – you choose which events send notifications and to whom. Notifications keep everyone informed without manual effort.
- Reporting and Analytics: Robust reporting is important. Check that you can easily pull reports on metrics like on-time percentage, average unload times, carrier performance, dock utilization, etc. The system should have an audit trail and possibly even a dashboard for live KPIs. Flexible reporting (e.g., export to Excel, schedule reports via email) is a plus, so you can share data with others or analyze it further.
- User Permissions & Ease of Use: The software should allow different permission levels (admin, scheduler, viewer, carrier, etc.), so you can control who sees or does what. It should also be user-friendly – think drag-and-drop calendar interface, intuitive navigation, and ideally mobile-friendly design for use on tablets or phones. A clean, modern interface reduces training time and user errors.
- Technology and Deployment: Consider how the software is delivered. The trend is strongly toward cloud-based (SaaS) solutions for dock scheduling, these require no hardware on your end, are accessible anywhere, and updates/support are handled by the provider. SaaS systems also tend to integrate more easily via web APIs. On-premise licensed software might offer more control in some cases but comes with IT overhead (servers, maintenance) and can raise security concerns when opening access to external users. Unless you have a specific reason for on-prem, a SaaS solution often provides the quickest time-to-value and scalability. In fact, SaaS dock scheduling can often go live in a matter of weeks and start delivering ROI fast compared to lengthy installations of traditional software.
Build vs Buy – Weighing Your Options:
One major decision is whether to build a custom in-house system or purchase a commercial solution. While building in-house might seem attractive if you have a very unique operation or idle IT resources, be cautious: developing your own dock scheduling software is a significant undertaking. Unless your company’s core competency is software development, the process can become costly and slow. You’d need to gather requirements, design and code the application (and a portal!), test it thoroughly, deploy it, and then continuously maintain and update it – all of which could take many months or even years. We’ve seen scenarios where internal projects fell behind schedule and by the time they delivered something, it was already out of date with modern web technology trends. Remember, a dock scheduling system today typically involves a web interface for external users; keeping that “future-friendly” and secure is no small task for an internal team to manage long term.
On the flip side, proven commercial solutions have entire teams of developers and industry experts who have been refining their product for years to handle a wide range of scenarios. The best dock scheduling software out there has evolved through feedback from hundreds of companies – chances are, your requirements are not as unique as you might think, and an off-the-shelf system can meet 95% of them (and often the other 5% can be tweaked or you may realize they’re not truly needed). By buying, you also benefit from continuous improvements and support that a vendor provides, rather than burdening your internal IT with endless enhancement requests.
Cost is another factor: building in-house is typically a large upfront cost (all those developer hours, infrastructure, etc.), whereas buying can often be an operating expense spread over time, especially with SaaS’s subscription model. SaaS models are “pay as you go” so you can start with lower risk and scale up. Plus, vendors often offer implementation services, best-practice advice, and have experience integrating with systems you use – accelerating the deployment. For example, a best-of-breed vendor with lots of integrations under their belt can simplify hooking into your WMS/TMS compared to you building from scratch and figuring out those APIs.
In short, buying a dedicated dock scheduling system is usually the smarter choice for most companies unless you have extremely specialized needs and a lot of IT muscle. It lets you reap the benefits faster and leverages the collective wisdom built into these products. As one expert quipped about companies thinking they’re totally unique: “I’ve got bad news – it’s not the case!” Meaning, the problems and requirements in dock scheduling tend to repeat across industries, and vendors have likely solved them already.
Other Considerations in Selection:
Once you decide to evaluate vendors, keep in mind factors beyond just features:
- Vendor Experience and Support: Look for providers who have been in this space for a while and have success stories in your industry. For instance, if you are a retailer or manufacturer, does the vendor have clients like you? Check for case studies. Also assess their support and onboarding process – you want a partner who will guide you through implementation and be there to answer questions, not just sell and disappear.
- Integration and API capabilities: As emphasized, ensure the vendor can integrate with your existing systems. Ask about standard connectors or API endpoints. A red flag would be a system that can’t easily import/export data or that forces you into rigid data formats.
- Scalability and Performance: If you have a high volume of appointments (say hundreds per day) or plan to grow, make sure the system can scale. Multi-site organizations should check that adding a new DC in the system is straightforward. Performance (load times, real-time updates) is important too – a laggy system would frustrate users, especially carriers using the portal.
- User Feedback: Try to get feedback from actual users – some vendors might connect you with a reference client. Alternatively, if you can do a trial or demo, involve the people who will actually use the system (schedulers, gate clerks, etc.) and get their opinions on usability.
- Cost Structure: Understand the pricing model – is it subscription-based on number of sites or appointments? Are there limits on users or carriers? What does implementation cost include? Compare the total cost of ownership with the expected savings. Often the cost will be a fraction of the savings from efficiency gains, but you’ll want to budget properly.
- Trial/Pilot Options: Some companies start with a pilot at one site or a limited scope to prove out the solution. This can be a wise approach – ensure the vendor supports pilot deployments that can later scale up, and that you won’t be stuck if you decide to expand.
Choosing the right dock scheduling system does require careful thought, but investing time in selection will pay off. The ideal solution will check the boxes on functionality, play nicely with your other software, and come from a partner with deep experience in dock operations. Do your due diligence, make use of resources like buyer’s guides, and envision where you want your warehouse operations to be in a few years. The right system should align with that vision and have the flexibility to grow with you.
10- How to Implement Dock Scheduling Successfully in 5 Steps
Convinced that it’s time to ditch the clipboards and embrace a dock scheduling system? As with any new software or process change, success lies in careful implementation and getting buy-in from your team and partners. Here are a few tips to ensure a smooth transition:
1- Involve Your Team Early:
Warehouse supervisors, receivers, shipping clerks, logistics coordinators – these are the people who will use the system daily. Engage them in the selection and design process. Their insight is invaluable for configuring the system (they know where the current pain points are). Plus, when people feel heard and see that the tool will make their lives easier (not harder), they’re more likely to embrace it. Highlight the benefits (fewer calls, no more tedious data entry, clear schedules every morning) so folks realize this isn’t just change for change’s sake but a real improvement.
2- Phase the Rollout:
If you operate multiple sites or many docks, consider a phased implementation. Start with one facility or a subset of docks to pilot the system, work out kinks, and learn what settings work best. This pilot can become the template for other sites. It also creates internal champions – once one location is succeeding (and bragging about their time saved or reduced wait times), other managers will be eager to get on board. A phased approach reduces risk and allows adjustments before company-wide deployment.
3- Set Clear Rules and Expectations:
A new dock schedule system will likely come with new rules for carriers and vendors. For instance, you might require that all appointments be made at least 24 hours in advance, or that any reschedule must be done through the portal (no more random calls to the warehouse floor). Communicate these expectations clearly to your partners. Update your routing guides or vendor compliance manuals if needed. Some companies even hold brief training webinars for their carriers to show them how to use the new dock application or portal. The smoother you make it for external users, the faster they’ll adopt it. Remember, the goal is to eliminate the old habits of just “showing up and hoping for the best” – everyone needs to understand the new process is digital and structured.
4- Monitor KPIs and Celebrate Wins:
Once live, keep an eye on key metrics to ensure the system is delivering. Track things like average truck turnaround time, % on-time arrivals, or the volume of appointments self-booked by carriers (a sign of engagement). Share improvements with the broader team – e.g., “Hey, we’ve reduced loading dock wait times by 30% in the first month!” or “Our warehouse handled 15% more shipments this quarter with the same docks, thanks to better scheduling.” Celebrating these wins boosts morale and reinforces the value of the new system. It can also help justify the investment to upper management by showing a clear before-and-after picture.
5- Continually Refine the Process:
Implementation isn’t one-and-done. Use the system’s analytics to identify areas to tweak. Maybe you notice certain hours are overbooked while others are underused – you can adjust your slot availability or staffing accordingly. Or you discover a carrier that frequently no-shows; maybe it’s time to enforce stricter penalties or have a conversation with them. Many companies find that once the baseline chaos is eliminated, they can focus on fine-tuning operations to really maximize efficiency. For example, you might move from two-hour default slots to more granular scheduling once you have confidence in the system’s data. Or integrate additional features like a delivery appointment scheduling software that ties into customer delivery scheduling (closing the loop from inbound to outbound planning).
Lastly, make sure to leverage support and training from your software provider. The best vendors are partners in your success – they’ll offer onboarding help, best practice guidance, and ongoing support. Don’t be afraid to ask questions or request features that you need; the industry is evolving, and good providers adapt to their customers’ needs (many great features come from user feedback, as seen in the earlier case study where a small configuration change made a huge difference).
Conclusion
Loading docks might not be the most glamorous part of a warehouse, but they can make or break your operation’s efficiency. The evidence is overwhelming – investing in a robust dock scheduling and management system turns what was once a logistical headache into a strategic advantage. By implementing warehouse dock scheduling software, companies are slashing wait times, boosting productivity, improving relationships with carriers, and ultimately saving money. In an era where every minute and dollar counts in the supply chain, leaving your dock schedule to clipboards or guesswork is no longer an option.
How C3 Solutions Can Help You Build Your Case.
-
Talk to our Experts! Request a personalized demonstration of C3 Reservations, our best of breed dock scheduling software, or C3 Yard, our award winning yard management software. Our product experts will walk you through the application via an online meeting center and answer your questions. Click here to request a demo!
-
Choose from a myriad of resources that will help you seal the deal with your decision maker - from White papers to case studies and industry-oriented programs (FOOD & Retail), we have +20 years of expertise ready to be shared among your peers so that you are Ready to Take it to the Next level.