Don't Schedule Another Delivery Until You've Fixed These 3 Mistakes
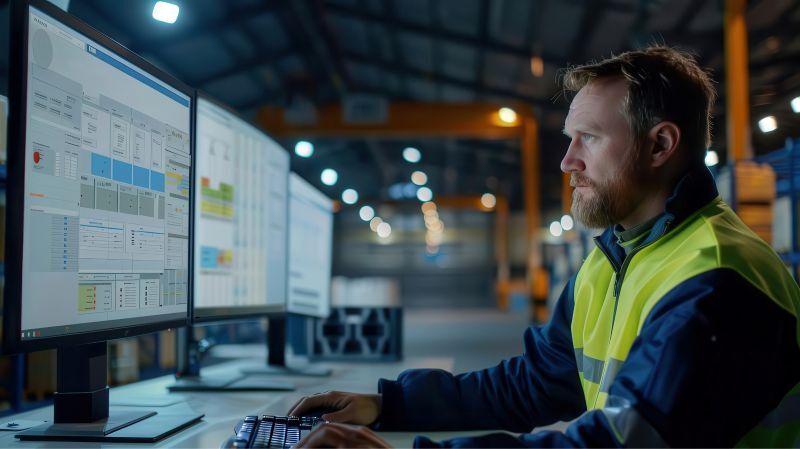
It's 8 a.m., and trucks are already piling up at your warehouse's gate. Drivers are waiting and losing patience, warehouse crews are scrambling, and your phone is ringing because a customer wants to know why their shipment is late. Sound familiar? If so, your yard process has cracks, and every new truck worsens them.
So, before you add another appointment to the calendar today, pause. In this article, we will discuss three common mistakes that keep yards and docks in constant chaos. We will also discuss how to fix them, slash wait times, shrink detention bills, and make everyone, from forklift drivers to customers, breathe easier.
Why do Yard Visibility and Dock Scheduling Matter?
Your inbound flow sets the tone for everything else. If trailers sit idle, your warehouse can't unload or replenish inventory on time. Finished goods miss their shipping windows if outbound trailers get buried behind inbound backups. Wait times exceeding two hours cost carriers $50–$100 per hour in detention fees, and the average U.S. driver now spends about 2.5 hours waiting per stop. Multiply that by five or six stops a week, and you've got a serious drain on capacity and morale.
The antidote? A tight yard-and-dock operation built on real-time data, intelligent scheduling, and cross-team communication. Let's dig into the three biggest mistakes standing in your way.
Mistake 1: Running the Yard Blind (No Real-Time Visibility)
Why It Happens
Many facilities still rely on clipboards or static spreadsheets. Once a driver checks in, someone marks "arrived," and that's the last live update anyone sees. Meanwhile, trailers get dropped wherever there's space, yard jockeys roam, and the dock office has no clue which container holds the urgent parts arriving today.
The Damage
-
Lost time: Crews burn 10–20 minutes per move hunting for trailers.
-
Dock jams: Unknown trailer status means you don't prep the right door.
-
Outbound delays: An empty trailer needed for shipping might be blocked by three others.
A survey found that fewer than 10% of managers are fully confident in their real-time yard data. Nearly half said that the location and availability of equipment are unclear on a daily basis.
How to fix it ?
Turn on the lights:
-
Adopt a Yard Management System (YMS). Modern YMS tools track trailer IDs via GPS, RFID, or barcode scan, then display them on a live yard map.
-
Automate the gate. Place a tablet or kiosk at check-in so drivers can capture key data, such as trailer number, load type, and appointment ID, immediately.
-
Push alerts. The system pings a supervisor if a trailer sits idle past its time limit, no more forgotten containers.
Payoff: Crews know precisely where to go, jockey moves drop, and your yard stops being a black hole.
Mistake 2: Chaotic Dock Scheduling (Spreadsheets + Hope)
Why It Happens
Schedulers juggle calls, texts, and emails, then paste everything into a color-coded sheet. Carriers quietly double-book slots "just in case," and shippers squeeze in late loads. Come Tuesday morning, five trucks show up for two doors at the same hour.
The Damage
-
Driver wait penalties: Detention kicks in fast, extra costs for you or the carrier.
-
Labor waste: Dock teams stand idle at 9 a.m., then drown at 11 a.m.
-
Safety risk: Crowded yards raise accident chances; each 15-minute delay raises crash risk by 6%.
A recent study found that 50% of carriers experience excessive wait times weekly. Drivers say they lose up to $1,500 a month in unpaid delay time.
How to fix it ?
Move to self-service, rules-based scheduling:
-
Single online portal. Carriers select open slots that meet your rules—load type, trailer length, live unload vs. drop.
-
Capacity controls. The system blocks overbooking. If you can handle four live unloads in an hour, a fifth requests auto-deflect.
-
Automatic updates. Late arrival? The carrier updates the ETA in the portal; alerts go to the yard, dock, and transport teams instantly.
Payoff: Arrivals are staggered, detention plummets, and staff workloads level out.
Mistake 3: Working in Silos (Yard, Dock, Transport Not Aligned)
Why It Happens
Different teams own different systems. The yard utilizes a whiteboard, the warehouse operates within a WMS, and transportation utilizes a TMS. Data stays trapped, and the phone tag fills the gaps.
The Damage
-
Mis-prioritization: A trailer holding "hot" parts gets parked in the far lot.
-
Outbound misses: The dispatch schedules a pickup, but the driver is unaware that the load hasn't been staged yet.
-
Finger-pointing: Yard blames dock, dock blames carriers—meanwhile, customers see a late delivery.
50% of sites have no link between the yard and WMS; another 30% have partial links that vary by shift. That's a recipe for crossed wires.
How to fix it ?
Break the walls:
-
Integrate systems. Your YMS should share the status with WMS and TMS. When a hot shipment arrives, the yard flags it, and the dock preps the door.
-
Shared dashboards. Monitors should be placed in a joint control room or virtual hub so that every team views the same queue in real-time.
-
Daily huddles. Five-minute stand-ups between the yard lead, dock supervisor, and dispatch align priorities.
Payoff: Everyone knows which inbound loads feed which outbound orders, ensuring trailers flow correctly.
Quick Word on Outbound
While this guide focuses on inbound fixes, the changes spill over naturally:
-
Faster turns free dock doors for loading outbound.
-
Integrated data lets transport teams book pickups when trailers are truly ready.
-
Happier carriers stay loyal, reducing re-rate risk.
Tuning inbound is the key that unlocks outbound rhythm.
A Little Math on the Payoff
-
Cutting the average wait time from 2.5 to 1 hour saves up to $75 in detention per truck (assuming a rate of $50 per hour after free time).
-
At 40 inbound trucks daily, that's $3,000 daily or about $750,000 a year.
-
Add labor gains: If dock staff reclaim 15 minutes per trailer search and handle five fewer searches a shift, that's 1.25 crew hours saved daily — roughly $30,000 a year in labor.
-
Combined with reduced fuel burn from less idling, fewer yard accidents, and better carrier rates, the ROI of fixing these mistakes is huge.
Ready to Clean Up Your Yard? C3 Solutions Can Help
If your team is done chasing lost trailers and juggling phone calls, it's time for modern tools. C3 Solutions offers yard and dock management software built for busy U.S. warehouses. Our platform gives you:
-
Real-time yard maps so no trailer is ever "missing."
-
Self-service dock scheduling that ends email chaos.
-
TMS/WMS integration to tear down silos.
-
Automated alerts to keep drivers and staff in sync.
Customers report up to 40% shorter wait times and 30% fewer yard moves within weeks. Want to see how it works? Book a quick demo and start fixing those mistakes today, before you schedule another delivery.