3 Essentials to Overcome your Dock Scheduling Madness
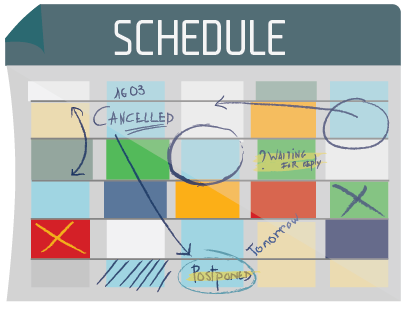
Docks, be they traditional warehouses, manufacturing sites, retail stores, hospitals or convention centers, can be very complicated to manage. At a high level, it’s simply about getting product in and out of the warehouse and turning drivers around as quickly as possible. However, the shear relative volumes and the numerous variables in play can quickly turn your dock operations into a complicated logistics operation. What are the symptoms that something is amiss in your dock operations? Can you identify the direct costs associated? What possible solutions exist?
Symptoms that your dock is a mess
The most common stories we hear can be summarized as follows.
-
Trucks arrive at anytime they want and this creates congestion in the yard
-
Although you schedule appointments for your docks, drivers don’t respect the appointment times. Similarly, the business allocates a broad delivery window (e.g., 6 hours) for the given delivery date; which is almost like not having an appointment.
-
The scheduler obtains incomplete information (e.g., only the carrier name). Details that can affect the time to unload (e.g., how much material is arriving, how it’s loaded, how many POs and line numbers) is critical to planning your dock schedule.
-
Lack of visibility on incoming shipments renders it difficult to plan for the appropriate labour; creating the need to pay for overtime labour
-
Multiple spreadsheets and calendars are being used, managed by several associates, causing confusion and a level of complexity that creates opportunities for errors that are reflected in the dock operations
-
Buyers place orders for goods to be delivered at the warehouse without taking into consideration capacity
The costs associated to poor planning and scheduling
Granted that few companies are able to ventilate the true costs related to inefficient dock operations (other than overtime labour), the last thing you want to do is to underestimate them, including:
-
Penalties for driver detention fees
-
Lost sales (e.g., weekly retail promotions, out of stock items) because of your inability to receive goods that are a priority
-
External storage is periodically required because you don’t have visibility on warehouse capacity relative to incoming volumes.
-
Carrier rates and cost of goods sold (COGS) are inflated to compensate for time wasted delivering to your warehouse.
-
Overtime labour paid to dock workers which can be eliminated by levelling out dock activities across the shift.
There is hope!
It all starts with a plan
Whether you’re currently allowing drivers to arrive on a first come, first serve basis or whether you’re currently scheduling loads, the first root cause to analyze is the absence of a plan. If you talk to any experienced scheduler, they’ll tell you how they spread the deliveries or pick-ups by order type, product type, complexity of unloading/loading, etc. They may also treat LTL, FTL, containers, rail cars differently. They already have a basis for a plan in their mind.
For certain sites, spreading the loads out evenly across the day may be sufficient. Others will need to restrict one container load per period of time, or certain products (e.g., water, paper, cosmetics). In the world of logistics, a schedule cannot simply be a replica of a traditional calendar format. You’re not simply booking a generic time slot. There may be multiple dimensions you need to take into consideration. You need to make a list of all the factors and variables that influence the time to turnaround a truck and find a dock scheduling system that will accommodate these.
Visibility is the key
Yet, despite their best efforts to plan and schedule the loads, we still receive inquiries from companies who admit to having issues with overtime labour, driver wait times and warehouse capacity issues. Why? The simple answer is visibility.
In a manual scheduling process, using a spreadsheet or paper calendar, the warehouse manager will have difficulty obtaining the data required to plan his labour count or even alert purchasing of an upcoming capacity issue at the warehouse. The challenge is intensified when you have more than one scheduler working on approving appointments across multiple sites. Businesses may ask the schedulers to enter appointment data in their WMS, ERP, TMS, providing some visibility but it will be restricted to the perspective offered by the given system. In other words, entering the PO numbers in the WMS with their respective quantities will not indicate how it is loaded (e.g., floor loaded vs. palletized) and therefore the visibility on the unload time or labour requirements is limited. Similarly, the TMS focuses on collect freight and will not provide a complete picture to include the prepaid freight and couriers, for instance. Loads that need to be staged is another great example. Which system will restrict the number of staged loads you can allow during a shift?
Therefore the ideal solution is to have a dock scheduling system that will integrate data with your other information systems, giving you the best of both worlds; an efficient planning tool with full visibility.
Managing Delivery Windows
I recently met a retailer who offers a six hour delivery window to their suppliers. This makes sense if you’re looking at it from a perspective of store replenishment. I fully understand that the business’ priority is to ensure the product arrives on a given day, received as inventory so the picking can start and the store replenishment objectives be attained. This is a basic concept in retailing. However, it sure doesn’t help the receiving team. This created peak receiving periods that contributed to driver wait times, overtime labour and an augmented stress level for the personnel managing the docks.
Without losing site of the ultimate objective (i.e., on time store replenishment), the dock scheduling system can manage the delivery window and also optimize the dock operations. A dock scheduling system like C3 Reservations can, in addition to reading the expected delivery date (EDD), also prioritize appointment times by interpreting various PO and appointment fields, applying specific business rules and constraints. Whether the delivery window is a broad rule that applies to all products or is PO specific, managing it effectively will go a long way to improving the fluidity of your dock operations.
The Next Steps...
If your dock is a mess, you’re not alone. Independent of the size of your company or whether you’re already scheduling appointments or not, the absence of a plan, visibility and a dedicated system is usually the root cause of your pain.
The next step towards resolving the mess in your dock operations is to take inventory of the following points.
-
What factors influence your dock operations? Specifically those you think should be part of the overall plan?
-
What constraints and rules do you need to apply to the factors that influence your dock operations?
-
Who are the actors/users in your supply chain and internally that should have visibility on the dock operations?
-
What are your receiving and shipping priorities?
-
With which information system, if any, should the dock scheduling system exchange data with?
-
Which reports and dashboards would be useful to measure dock productivity and key performance indicators?