A Day Without vs With a Yard Management System
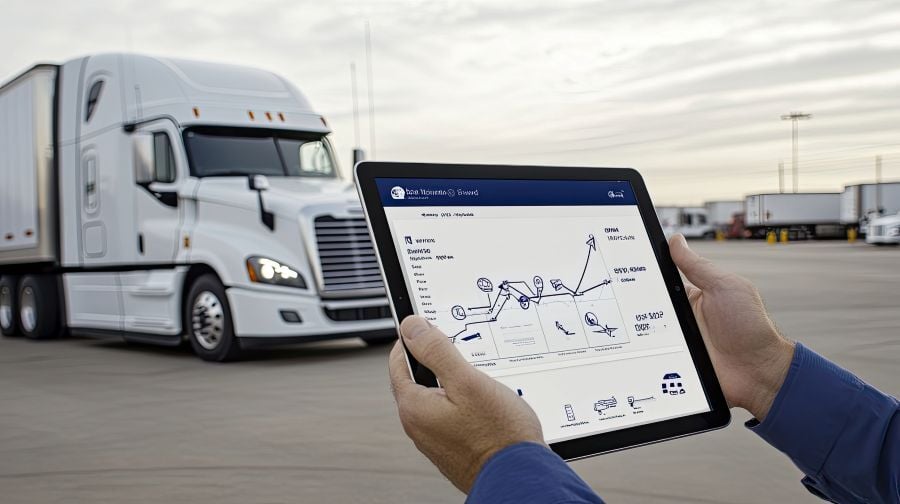
If you've ever spent time in a traditionally run, busy warehouse or distribution center, you've probably seen the chaos that can build up in the yard. Trucks can show up at any time, sometimes all at once.
Technology has sorted out many supply chain processes. So, what's the answer here? The answer is a Yard Management System (YMS) that can address all these issues and streamline the in-plant logistics process.
In this article, let's gain a deeper understanding and try to visualize the differences between a traditional warehouse and a modern warehouse with YMS.
But first, let's understand YMS well.
What is a Yard Management System (YMS)?
A YMS is an in-plant logistics solution that helps manage the flow of trailers, trucks, and goods through your facility's yard.
A Yard Management System helps companies to:
- Track all trailers and containers on the property
- Speed up check-ins and check-outs
- Coordinate dock scheduling between the warehouse and drivers
- Reduce wait times and detention charges
- Help with easy reschedules and avoid costly miscommunications
- Integrate with existing systems like TMS and WMS to make the overall supply chain integrated
It's like having a control tower for everything that moves in and out of the warehouse, keeping track of who's arriving and when, where trailers are parked, which docks are free, and what needs to move next.
With that in-depth understanding of the YMS, let's understand how daily operations differ when you have a YMS versus when you don't.
A Day Without a Yard Management System
6:00 AM – The Line Starts Early
Drivers start showing up for their morning appointments. But, there's already a jam at the gate instead of a smooth process. Security guards are flipping through papers, trying to match a truck number with a scheduled delivery. Phones are ringing. Everyone's trying to confirm who's who.
One driver says, "I've been here since 5:50." But without real-time visibility, no one can confirm it quickly.
8:00 AM – Docks Are Backed Up
Inside the yard, it's no better. Three trailers have been directed to the same dock. Warehouse staff are unsure who goes first, and the forklift drivers are sitting idle. Another trailer with time-sensitive goods is still in the lot, and no one can find it.
You overhear a supervisor say, "If we don't find that trailer soon, we'll miss the cut-off."
10:30 AM – The Hunt for a Trailer
Someone finally notices that trailer #237, the one with the high-priority load, is missing. A yard jockey starts walking row to row with a clipboard, asking others if they've seen it. It turns out it was parked in the wrong row, and no one updated the spreadsheet.
1:00 PM – Delays Pile Up
Carriers are now waiting longer than planned. A few have already left without unloading because they can't wait anymore. Detention charges are starting to pile up. The warehouse team is pressured to catch up, but there’s no organized plan.
4:00 PM – Still Behind Schedule
The yard is full. Trucks are waiting to unload, while others are waiting to exit. The warehouse manager has no idea what is ready and what is not, and is still relying on outdated spreadsheets. Everyone is trying to do their best, but without the right tools to help, things remain constantly reactive.
6:00 PM – Burnout and Bottlenecks
It's the end of the shift, but no one feels done. Shipments are late, people are frustrated, and the yard still resembles a jigsaw puzzle that no one can solve. It will still take a few hours for the work to be finished. Now, overtime has started, while demurrages have been continuing since morning.
A Day With a YMS: Like Clockwork
So, while we saw how stressful a day can be with traditional yard management methods, let's also look at what changes and how with a YMS.
6:00 AM – Check-ins are Click-and-Go
Drivers check in using a mobile app or kiosk at the gate. The YMS automatically verifies their appointment, assigns a dock, and sends instructions. The gate team doesn't need to play the traffic management game — they can manage with a few clicks or with an Automated Number Plate Recognition (ANPR). They just focus on other responsibilities while the vehicles check in on their own.
No paper. No chaos. It's just a smooth entry.
8:00 AM – Dock Flow is Smooth
Each dock has a clear schedule. Forklift drivers know what's coming and when, and there's no confusion about who gets which dock or in what order.
Trailer #237? Already docked. The inventory team is unloading as scheduled. YMS integrated with WMS enables easy racking for the unloading team. GR is done with integrated ERP, and the turnaround is completed before the scheduled time, all paperless.
10:30 AM – Real-Time Trailer Tracking
Need to find a trailer? Open the yard map on your screen. Every trailer is tagged and color-coded. The yard jockey heads straight to where it is. No walking in circles. No radio chatter. No wasted time.
1:00 PM – Appointments Adjust in Real-Time
One carrier shows up 30 minutes late. The YMS auto-adjusts the schedule and shifts another ready trailer into its dock slot. The delayed truck checks in without any manual efforts or coordination. After automated entry with ANPR, it is directed to the integrated weighbridge so that everything is kept ready while its revised turn arrives. Everyone stays productive, and there's no idle time.
4:00 PM – Yard is Balanced
By the afternoon, the YMS had already helped rotate full trailers out and brought in empties. The yard feels well-oiled and organized, not crammed. Dwell times are down. Everyone knows what's happening, and things are running on time. Any questions? Just check the system.
6:00 PM – On Time, Under Budget
The last trucks roll out. There are no surprise detention charges. No overtime for warehouse staff. The system has already generated a report displaying KPIs for the day, including trailer turnaround time, dock utilization, idle time, and more.
Now, that's how you wrap a shift like a pro with a YMS.
Why It Matters: The Real Cost of No YMS
Let's break it down. Without a YMS, your yard could cost you in ways you don't even realize.
-
Detention Fees: Carriers charge by the hour when stuck waiting. That adds up fast.
-
Wasted Labor: Yard jockeys spending 30+ minutes to find one trailer? Multiply that across a week.
-
Dock Bottlenecks: When docks aren't scheduled well, staff sit idle or rush at the last minute.
-
Lost Visibility: Managers can't fix what they can't see. Without data, it's all guesswork.
-
Frustrated Drivers: Poor yard flow hurts your career relationships — and may get you deprioritized.
6 Benefits of a Yard Management System (YMS)
Here's a quick look at what you gain with a good YMS:
Benefit |
What It Means |
Real-Time Visibility |
Know where every trailer is, instantly |
Faster Gate Processing |
Check-ins done in under 2 minutes |
Better Dock Scheduling |
No more double-bookings or idle docks |
Trailer Turnaround Tracking |
Track dwell times and speed things up |
Alerts & Notifications |
Be proactive, not reactive |
Audit Logs & Reports |
Get proof of what happened, when, and why |
Partner with C3 Solutions for Smarter Yard Management
If you're still juggling clipboards, spreadsheets, and two-way radios, it's time for a change. C3 Solutions offers Yard Management Software that brings visibility, control, and efficiency to your yard operations. With our solution, you can:
- Cut detention fees
- Streamline truck movements
- Eliminate trailer search time
- Optimize dock schedules
- Gain insight from real-time dashboards
Whether you're running a busy warehouse, a distribution hub, or an extensive DC network, we've got the tools to help you run your yard smarter, not harder.
Ready to see how much better your day can be with a YMS? Talk to C3 Solutions today. Let's build a yard that works for you.