What is Queue Management, and Why Does It Matter?
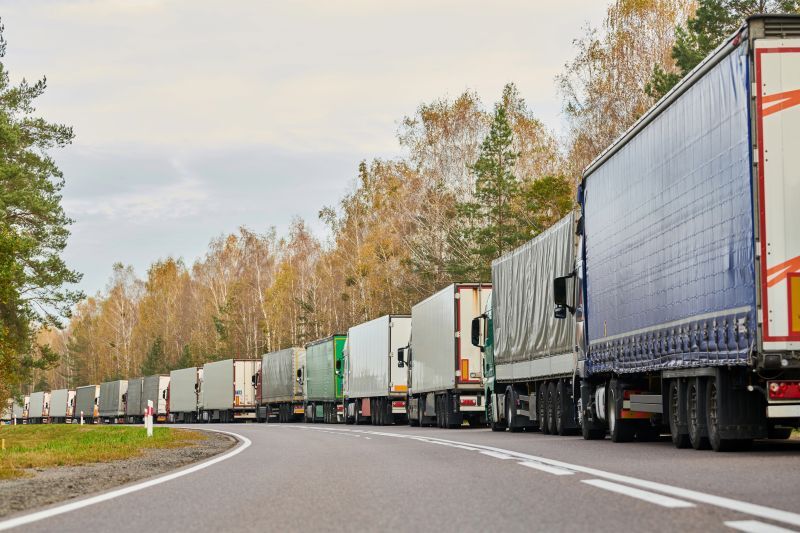
In the supply chain and logistics, effective queue management has far-reaching effects that are not felt immediately. At a busy warehouse dock, when multiple trucks arrive simultaneously to drop off or pick up goods, the result can be prolonged wait times, disrupted delivery schedules, increased storage costs, and higher labor expenses due to overtime.
To manage this, assigning staggered and individual time slots ensures a steadier flow of arrivals, allowing each vehicle to be served promptly. This approach simplifies operations, reduces overhead expenses, and satisfies everyone — suppliers, warehouse staff, and end customers.
If you're new to queue management in supply chain, don't worry. This guide will explain queue management in the context of supply chain and logistics, why it matters, and how to implement it effectively. We'll look at simple examples, common challenges, and best practices. By the end, you'll understand how strategic queue management can give your business a competitive edge.
What is Queue Management?
Queue Management in the supply chain refers to the systematic organization of waiting tasks, like trucks at docks or items at inspection stations—to reduce delays, control costs, and improve throughput. By assigning time slots, monitoring wait times, and reallocating resources in real time, companies can prevent bottlenecks and enhance operational efficiency. Effective queue management reduces lead times, labor expenses, and safety risks while improving delivery reliability and customer satisfaction. As Gartner notes, “queue optimization plays a crucial role in supply chain agility and execution excellence” (Gartner, Supply Chain Strategy Report, 2023).
When we talk about queue management in a supply chain context, we often think about situations where goods are entering or leaving a facility — like trucks arriving at a warehouse loading dock, ships waiting for a berth at a port, or containers queued at a yard waiting to be picked up. However, it can also apply to internal operations, such as products waiting at a quality inspection station inside a factory.
Queue Management in the Bigger Supply Chain Picture
Excellent queue management isn't and can't be an isolated optimization effort. It is part of a broader supply chain optimization to improve dependability, customer value, and efficiency. If done properly, it has far more significant business impacts. If queues are properly managed, shipments move much more smoothly, warehouses operate better, and trucks stay on the road longer, delivering goods rather than patiently waiting in a line.
Queue management will eventually deliver consistent lead times, reduce inventory carrying costs, and enhance overall supply chain productivity. These benefits also help develop great relationships with vendors and clients, get preferred pricing contracts, build brand equity, and position your company as a leader in the industry.
Why Does Queue Management Matter?
So, while we all hate waiting in queues, why does it matter for the supply chain? After all, the products will still eventually come out of the queue, right?
Wrong.
Queue management can be the difference between a predictable and unpredictable supply chain. It can be the difference between meeting or missing the customer timelines. Let's understand better how queue management can help a supply chain:
Improved Efficiency
Long, unmanaged lines lead to unproductive and wasted time, adding to the longer lead times. For example, if trucks queue endlessly at a distribution center due to poor scheduling, warehouse teams may scramble to unload one vehicle while others sit idly waiting. Proactively managing the queue has many benefits, such as pre-scheduled arrivals, reduced waiting times, and maximized throughput.
Cost Savings
Unnecessary waiting is expensive in supply chains. Consider a scenario where a truck driver waits an extra hour due to poor dock scheduling. That extra hour is not just lost productivity; it can also mean additional labor costs, potential late fees, and higher fuel consumption. Queue management helps minimize these hidden costs.
Better Customer Satisfaction
Whether a retail shopper is waiting in line or a supplier is waiting for unloading at a warehouse, nobody likes to wait longer than necessary. Well-structured queue management leads to shorter waiting times, better transparency, and happier stakeholders. In supply chain terms, this can translate to improved business relationships, more reliable deliveries, and greater loyalty from partners and customers.
Enhanced Safety and Compliance
At busy facilities, crowded yards and loading areas can pose safety risks. Unplanned trucks that may park randomly can lead to congestion, accidents, and unsafe working conditions. Effective queue management ensures orderly movement, reducing the risk of accidents and improving compliance with safety regulations.
Data-Driven Decision Making
Modern queue management systems often provide real-time data and analytics. By tracking how long vehicles or goods wait at various stages, businesses can start to understand the bottlenecks and implement improvements. Over time, analyzing these trends can lead to more accurate forecasting, better staffing decisions, and refined scheduling strategies.
5 Ways to Become Better and Effective at Queue Management?
So now we understand the importance of queue management in supply chain quite well. But how can the businesses become better at it? Here are the top 5 recommendations for improving queue management in supply chain:
1- Improve Forecasting
One of the first steps in managing queues is accurately predicting demand. This might mean analyzing historical data for warehouses and transportation hubs to see the peak hours trends. For example, if you know that most trucks arrive between 9:00 a.m. and 11:00 a.m. on Mondays, you can prepare additional staff or schedule time slots differently.
2- Capacity Planning
After assessing the arrival trends, understand your capacity. The crucial data points are how many customers you can serve per hour or how many trucks you can unload each day. If you know your dock can handle unloading two trucks per hour, avoid scheduling three trucks to arrive simultaneously. Capacity planning ensures that demand never overwhelms supply.
3- Scheduling and Reservations
Consider adopting a reservation system, especially for high-demand resources. By assigning time slots to each arriving truck, you create a controlled flow. This approach prevents crowding and gives everyone more predictability and control.
4- Real-Time Tracking & Communications
Technology solutions such as Yard Management Systems (YMS), Warehouse Management Systems (WMS), and Transportation Management Systems (TMS) can offer real-time visibility into queues. Knowing precisely how many trucks are awaiting and exactly where each shipment is in the flow helps managers make fast decisions to ease congestion. Real-time communication through these solutions could be life-changing. For instance, drivers who receive text notifications when their turn in a loading dock is due can better schedule their time.
5- Continuous Improvement
Queue management isn't a one-and-done thing; you must deal with the issue while running the operation. It is a continual process. Examine performance like wait times, peak loads, and employee utilization, which are frequently areas of improvement. Treat queue management as a continual improvement procedure for a smooth, long-term operation.
Queue Management in the Future
As supply chains grow more complex and global, the importance of effective queue management will only increase. Today, supply chains have more players than ever — multiple carriers, cross-docks, transshipment points, and distribution centers spread across different regions. Demand for sophisticated queue management tools like YMS, WMS, or TMS, along with queue management strategies, will rise further.
Upcoming queue management trends include automatic or AI-led yard management, dock appointment scheduling, and powerful routing based on real-time information that can understand the context, chat with the drivers, and take action automatically. However, companies must start creating the baseline for an effective queue management system today to reach there.
Ready to Transform Your Queue Management?
Queue management might look like an easy concept to master — just arrange lines so that they operate efficiently. However, beneath that, simplicity is a whole operational discipline. By managing queues well, you can boost efficiency, save money, enhance safety, and delight customers and partners. Whether you own a retail store or a worldwide distribution system, the principles remain the same: balance supply with demand, improve communications and visibility, and concentrate on continual improvement.
Recall that the objective isn't to eliminate waiting (which is usually not feasible and will start leading to capacity losses) but to make any waiting that occurs as organized, transparent, and short as possible. With the right preparation, proper IT solutions, and the flexibility to change, queue management could be your business's competitive edge.
At C3 Solutions, efficient queue management begins with the proper tools and experience. Our advanced solutions empower companies to control their performance, automate workflows, and decrease wait times. Supported by experts with proven success, we're with you every step of the way.
Do not let inefficiencies hold you back. Contact C3 Solutions today to learn how our customized queue management can help your company succeed.