7 Proven Dock Scheduling Strategies for Seamless Logistics
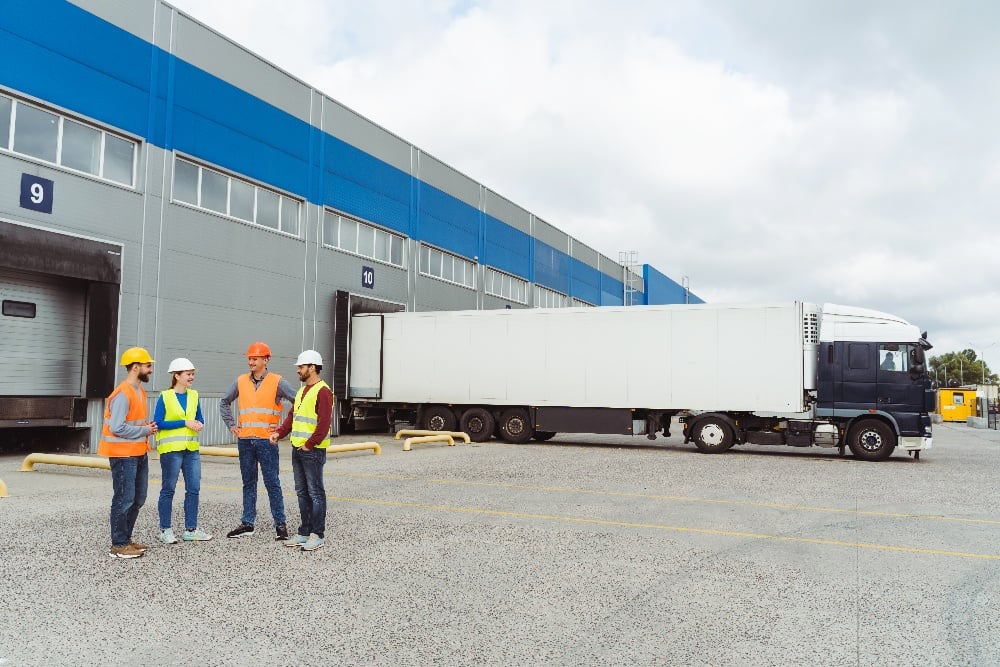
Efficient dock scheduling has become essential to supply chain management and logistics. It has gained popularity because it provides excellent convenience to all stakeholders, including dock operators, warehouse managers, and carriers.
Optimizing dock appointments significantly boosts operational throughput, slashes wait times, and boosts customer satisfaction as the products arrive on time with minimal delays.
The ecosystem of shippers, carriers, warehouses, vendors, and customers has evolved into strategic partnerships within the global supply chain. With all stakeholders focusing on technology, the global supply chain operates seamlessly, like clockwork.
To maintain this precision, logistics operations are tightly integrated with dock schedules and related internal processes, making meticulous planning and management of dock activities crucial.
Hence, building and following best practices in dock scheduling is necessary for an efficient supply chain. It streamlines operations and fosters a more efficient and lean supply chain.
This article will discuss seven strategic approaches to refine the dock appointment scheduling process, aiming for seamless operations like a well-oiled machine.
1. Implement Flexible Scheduling Options but Clear & Standard Policies
Flexibility in scheduling can significantly improve dock utilization and efficiency. Consider implementing strategies such as open scheduling windows or allowing drivers to book, modify, or cancel appointments through a mobile application.
This helps you get the latest updates from the truck drivers and improves their satisfaction by reducing waiting times. Flexible scheduling options help keep the schedule updated in real time and optimize the flow of goods in and out of your facility.
While providing flexible scheduling options is vital, so are developing and enforcing clear guidelines for scheduling and handling appointments.
This includes setting precise check-in and check-out procedures, defining late or no-show policies, and specifying loading and unloading times. Well-documented procedures ensure consistency in operations and help mitigate disputes or confusion among carriers and dock staff.
2. Prioritize Real-time Communication and Collaboration
Effective communication is the backbone of successful dock scheduling. It is critical for carriers and drivers on the move, as time is currency.
The top priority should be building clear and effective communication channels among all stakeholders, including warehouse staff, transportation managers, and drivers.
Companies should utilize platforms that provide real-time updates and alerts to ensure everyone is on the same page.This strategy minimizes confusion and delays and enhances your operations' adaptability to handle unexpected scheduling changes.
3. Analyze and Optimize with Data-Driven Insights
The power of data helps dock scheduling provide valuable insights that transform a company's logistics. By systematically collecting and analyzing critical data such as dock utilization rates, turnaround times, peak periods, and recurring bottlenecks, companies can unlock a wealth of insights to refine their scheduling practices.
Implement extensive data gathering across all parts of dock operations. This includes not only the timing and duration of each appointment but also the specific characteristics of the shipments, such as cargo type and volume, carrier performance, and delays or disruptions.
Monitor the performance with customized KPI dashboards. Analytics tools can then be used to deep-divide this data. These tools can run predictive analytics based on historical patterns, forecasting future dock scheduling requirements. Companies should use these insights to refine and optimize their dock scheduling strategies.
For example, if data shows recurring delays during certain times of the day or with certain types of cargo, adjustments can be made to the scheduling protocol or resource allocation to address these issues.
Tools like C3 Reservations offer analytics capabilities that help you understand patterns and trends. These capabilities allow you to make informed decisions that streamline operations and improve scheduling accuracy.
4. Integrate with Broader Supply Chain Management Systems & External Stakeholders
For dock scheduling to really shine in providing maximum efficiency and effectiveness, it must be integrated with the other planning & execution systems.
Integrating your dock scheduling system with the rest of supply chain management platforms, such as WMS and TMS, enables a seamless information flow across the chain.
It ensures that each component of the supply chain is aligned — from inventory levels and warehouse operations to transportation logistics and delivery timelines.
For example, real-time data from the TMS can inform dock scheduling systems of incoming shipments, allowing for dynamic adjustments to the schedule based on actual transportation conditions.
Similarly, integrating with the WMS ensures that the goods are ready and staged for loading or unloading as soon as the transport arrives, minimizing wait times and streamlining operations.
Extending integration beyond internal systems to include external partners such as suppliers, carriers, and logistics service providers further amplifies the benefits. This external integration allows all parties to access critical scheduling information, adjust to real-time changes, and collaborate more effectively.
For instance, carriers can receive instant notifications about schedule changes or specific loading dock assignments through a shared platform, helping them plan their routes and schedules more efficiently.
Such comprehensive integration optimizes dock operations and enhances the overall agility and responsiveness of the supply chain. This leads to improved service levels, reduced costs, and increased customer satisfaction.
5. Integrated Workforce Planning with Dock Scheduling
Integrating automated scheduling systems with labor management helps optimize workforce planning in sync with dock scheduling activities. This approach involves selecting a system that aligns well with existing Warehouse Management Systems (WMS) and Human Resources Management Systems (HRMS), ensuring seamless data integration and customization to fit unique operational needs.
By forecasting labor demand based on real-time dock activity data, these systems can dynamically allocate staff to specific docks or tasks, considering each worker's skills and compliance with labor regulations.
This integration allows for real-time adjustments to the workforce in response to unexpected changes in the shipping schedule, enhancing operational efficiency and reducing downtime.
The benefits of an integrated workforce planning system are many:
-
It aligns staff schedules with dock activities, significantly reducing wait times and speeding up cargo handling. It also optimizes resource utilization and reduces labor costs.
-
It ensures compliance with labor laws and improves workplace safety, thereby avoiding legal penalties and enhancing the company's reliability.
-
Predictive analytics from these systems aid in making informed decisions about operational improvements and workforce needs.
-
Fair and predictable work schedules foster higher job satisfaction and employee retention, contributing to a more motivated workforce.
This strategic approach boosts operational efficiency and supports a more adaptable and competitive business model.
6. Implement Rigorous Milestone Tracking & Continuous Improvement
"You get what you measure" is particularly true in dock scheduling. Systematically recording the date and time stamps for arrivals, departures, and loading milestones lays the foundation for analyzing and enhancing key performance metrics such as on-time arrivals and average turn-times.
Also, maintaining detailed records of these events proves invaluable when assessing carrier demurrage charges and calculating employee overtime costs, ensuring that every element of the dock scheduling process is thoroughly documented and monitored for efficiency.
Regularly review your dock appointment scheduling processes and solicit stakeholder feedback to identify areas for enhancement. Embrace innovations and adjustments that can refine scheduling practices and adapt to changing business needs.
7. Leverage Technology for Enhanced Efficiency
Relying on manual scheduling methods is akin to navigating a busy highway with an outdated map in today's digital age. Implementing advanced scheduling software, like C3 Solutions' sophisticated systems, transforms the dock scheduling process.
These technologies offer real-time updates, automated scheduling based on cargo and dock availability, and predictive analytics to foresee potential bottlenecks before they disrupt operations.
Build your own Dock Scheduling Strategy with C3 Solutions
Efficient dock appointment scheduling is often overlooked but is a critical element of modern-age logistics. These seven strategies provide companies with ways to enhance operational efficiency, improve stakeholder satisfaction, and gain a competitive edge.
C3 Solutions is the go-to choice of leaders for providing innovative tools and insights that empower businesses to master the art of dock scheduling. Reach out today to learn how these strategies can transform your logistics into an industry benchmark of efficiency and reliability.