5 Powerful Facts About Supply Chain Integration You Probably Didn’t Know
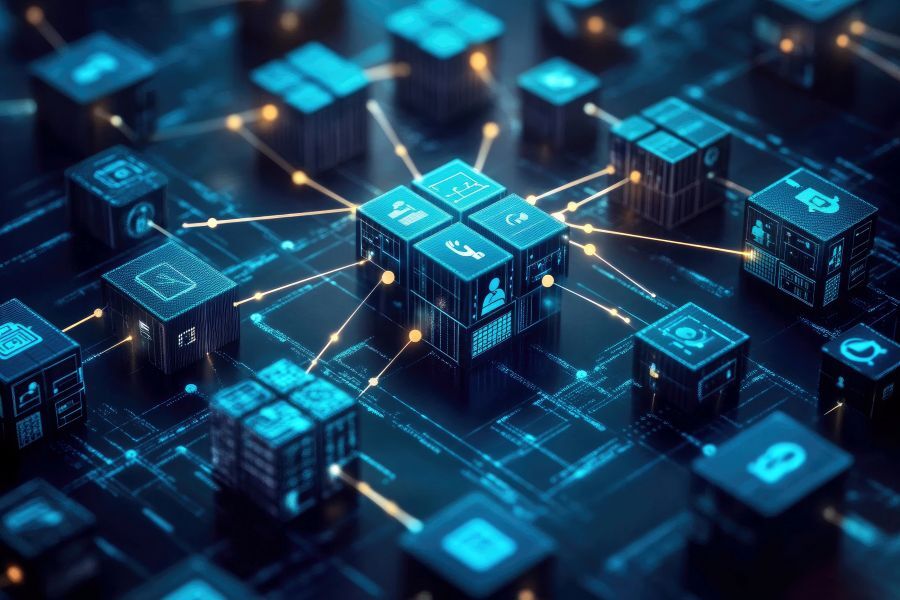
A Comprehensive Guide to Understanding Supply Chain Integration
Any supply chain has three kinds of flow:
- The flow of products
- The reverse flow of money (from customer to supplier)
- The flow of information
At times, information flow can be more critical than the product flow itself, as it keeps the stakeholders aware of what to expect. This one factor alone can differentiate a winning and a losing supply chain.
Supply chain integration (SCI) is a critical aspect of information flow, enabling data and insights to move through the supply chain. With supply chain solutions becoming increasingly ubiquitous and digital, companies can no longer afford siloed operations with stakeholders within and outside their processes.
This article will explore the concept of supply chain integration, why it matters, and practical ways to achieve it. First, let's understand what supply chain integration means.
What is Supply Chain Integration?
Supply chain integration is the method of aligning and synchronizing all the various components within the supply chain, including suppliers, manufacturers, warehouses, distribution centers, and even customers, through a seamless information flow.
Types of Supply Chain Integration
The SCI aims to automate processes, improve communication and collaboration, and establish a single, end-to-end system whereby data can move seamlessly and freely with all supply chain phases.
There are two primary types of supply chain integration:
-
Internal integration: Internal integration refers to integrating the teams within the business, like finance, sales, supply chain, production, procurement, and others, into one view for information sharing.
-
External Integration: Here, the integration goes beyond the company walls to include the other stakeholders of the company's supply chain, such as suppliers, 3PLs, and clients. External integration aims to share information among all supply chain participants.
While the explanation of types of integration is relatively easy, the data shared in these two types of integrations is entirely different. Almost all sorts of data can be shared internally. However, the integration strategy has to be well thought out externally so that all the stakeholders gain maximum visibility without sharing sensitive information.
So, let us understand the fundamental building blocks of the supply chain integration strategy.
Building Blocks of Successful Supply Chain Integration Strategy
Achieving seamless supply chain integration involves several critical components that should be in focus:
-
Create the detailed process as-is and to-be blueprints
The company should have a detailed process blueprint for the integration journey. The integration strategy should start by answering the as-is processes and what these processes should turn into after the integration is completed. This provides a clear picture to all the stakeholders and helps to remove inefficiencies that have crept in over the years. The to-be processes should be designed with unconstrained thinking.
-
Add Technology Components and Design Systems Integrations
Technology plays a vital role in supply chain integration. Once the to-be process blueprint is ready, start adding the existing technology components. This way, it will be easy to find out the gaps. Fill the gaps with aligned advanced digital tools, such as advanced planning tools (o9, Kinaxis, BY, IBP, etc.), Transportation Management Systems (TMS), Warehouse Management Systems (WMS), Dock Scheduling (DSS) or Yard Management Systems (YMS) or and more.
The aim should be to create a unified platform where data can flow seamlessly between departments and external partners. To make a future-ready strategy, include the next-gen elements in the strategy, like Internet of Things (IoT) devices, cloud computing, and blockchain technology. So, while some of these solutions can be unaffordable or nascent today, incorporating them later can improve the overall process.
-
Build a Data Standardization Strategy
Data standardization is crucial for ensuring that all systems across the supply chain can communicate effectively. When data is shared between different systems and in various formats, it leads to data losses, errors, and system inefficiencies. Creating standardized data storage, sharing, and reporting protocols ensures data standardization and accuracy throughout the supply chain.
For instance, Electronic data interchange (EDI) systems allow for the smooth transmission of purchase orders, invoices, and shipment notices between partners. This reduces manual intervention and speeds up processes.
-
Start with Agile Development and Build a Continuous Feedback Loop
The supply chain integration strategy should be realized via agile integration development. It allows for the building and pause of a mechanism instead of a one-time exercise. This provides continuous monitoring and improvement of integrations. Companies should regularly assess their integration performance through key metrics improvements like order fulfillment rates, lead times, and cost savings. By identifying areas for improvement, businesses can make incremental changes that lead to better overall performance.
Why Does Supply Chain Integration Matter?
Supply chain integration is not just about seamless end-to-end dataflows. It unlocks value and provides what the companies expect from today's supply chains:
- Improved Efficiency
- Complete Visibility
- Better Responsiveness
- Lower Costs
- Customer Delight
Now let's understand these in more detail:
1. Improved Efficiency
Synchronizing all components of the supply chain eliminates ineffective delays, redundancies, and bottlenecks. Integrating systems offers much better coordination and real-time visibility to inventory, production schedules, and transportation routes. This allows quicker decision-making and smooth supply chain movement of goods.
2. Complete Visibility
Integrated systems provide companies with complete visibility of different supply chain data points, like inventory levels, demand forecasts, and order statuses throughout the supply chain. This helps businesses make better choices and react fast to market changes.
For instance, real-time visibility into inventory helps companies avoid overstocks or stockouts while minimizing lost product sales and excess carrying costs. Likewise, integrated demand forecasting helps businesses adjust manufacturing times to meet customer demand better.
3. Better Responsiveness
With an integrated supply chain, businesses are better positioned for unexpected situations, like supply interruptions, demand variations, or new industry trends. Integration-led better responsiveness enables enterprises to rapidly adjust manufacturing schedules, supply alternative suppliers, or reroute deliveries. This agility helps companies avoid costly disruptions and ensure continuous operations even during uncertainty.
4. Lower Costs
An integrated supply chain can save organizations a great amount of money. Integration eliminates manual data management, like Excel uploads, downloads, and other repetitive tasks, reducing human error. Also, companies can optimize inventory levels, remove NVAs, and lower costs of logistics.
In a fully integrated system, procurement teams can also negotiate better terms with suppliers using historical order volumes and delivery times data. This increased bargaining power further drove down costs.
5. Customer Delight
Supply chain integration enables businesses to provide better customer service. With visibility into every supply chain step, companies can offer customers accurate delivery dates, real-time tracking, and faster response times to questions
Additionally, improved departmental coordination ensures orders are completed accurately and on time, minimizing the risk of errors, returns, and customer dissatisfaction.
Build Your Integrated Supply Chain with C3 Solutions
An integrated supply chain is an essential requirement for companies to compete today. Features like end-to-end data synchronization, real-time data, collaborative responses, and predictive analytics combine to unlock value, reduce costs, and create an excellent customer experience. But all of these can be enabled on the back of a strong integrated supply chain system.
At C3, we build next-gen supply chain solutions that integrate data, processes, and systems for true end-to-end visibility.
Our digital supply chain expertise across automation and digital integration gives you the tools and strategies you need to succeed. Our solutions simplify your processes while enabling your teams to make better, data-informed decisions. Whether you need to optimize your supply chain, increase agility, or enhance customer experiences — C3 Solutions is your partner for a future-proofed integrated supply chain.
Reach out to us today and embark on a journey toward supply chain efficiency, lower costs and end-to-end visibility.