The Role of Predictive Analytics in Improving Dock Scheduling
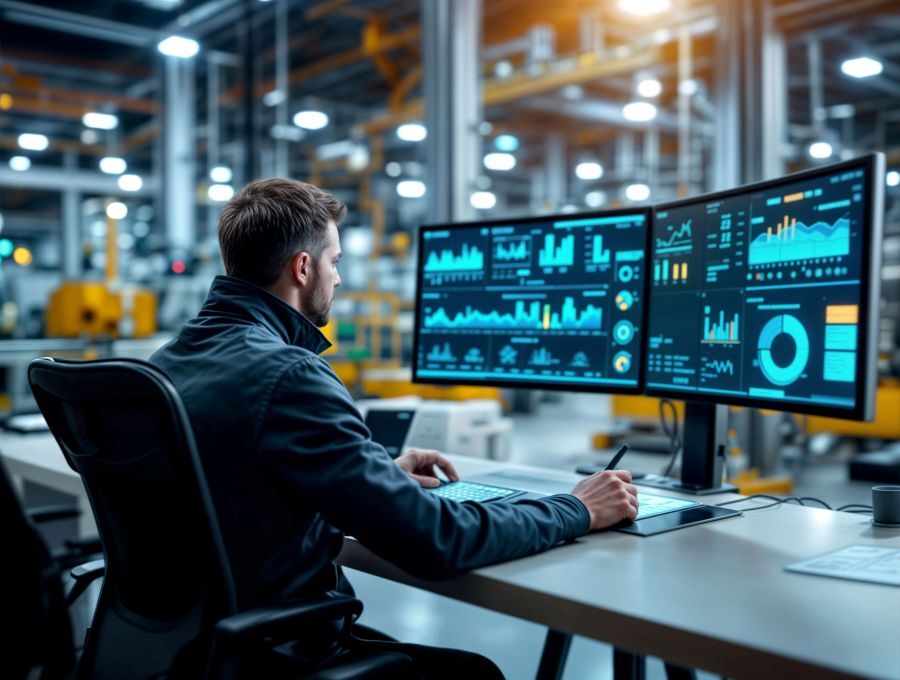
Dock scheduling software has seen huge leaps in the last few years with predictive analytics emerging as one of the most exciting advancements to date. Not only does it leverage big data to better understand prior operations, but it uses these insights to then forecast where things are headed for logistics and supply chain operations.
The result of this? Far more accurate dock scheduling.
In this article, we’ll break down exactly what predictive analytics are, the role they can play in dock scheduling, the benefits they offer, and key metrics that are needed for accurate analytics to happen in the first place.
Understanding the Basics of Predictive Analytics
At its most basic level, predictive analytics uses large amounts of historical data to answer the question, “What might happen in the future?”. It’s what the weather app on your phone uses to forecast the chance of rain next week, and it’s also what many logistics companies are using to create a more predictive supply chain.
Some predictive analytics tools rely solely on historical data and statistical algorithms for their forecasting, while others combine it with AI and machine learning technology to boost predictive abilities and pattern recognition.
5 Key Roles of Predictive Analytics in Dock Scheduling
Getting a chance to see ahead opens a world of possibilities in terms of more efficient and accurate dock scheduling. Here are 5 key roles that predictive analytics can play in creating a more streamlined dock scheduling process:
-
Demand Forecasting: One of the great frustrations of managing a dock schedule is how inconsistent demand can be. Just when things seem to be in a predictable rhythm, something changes seemingly without warning. Predictive analytics demystifies these issues by using historical data to forecast demand patterns and give logistics operations a better sense of what their incoming and outgoing shipment volumes are likely to be.
-
Capacity and Resource Management: The ripple effect of more accurate demand forecasting is that it also allows for better resource optimization. Predictive analytics can even be run solely on showing how much labor, dock space, etc. will be needed over different periods so that businesses avoid being understaffed or wasting valuable load space.
-
Avoid Delays: Demand forecasting already helps reduce wait times in a dock schedule, but predictive analytics can also be used to identify common causes of delays and as such, makes it easier to avoid them.
-
Quick Adjustments: A robust predictive analytics system will constantly adjust its forecasting according to real-time data. The outcome of this is more responsive dock scheduling practices that avoid getting stuck in lags.
-
Risk Management: Bad weather, traffic, and market dips can completely upend even the most tightly run dock scheduling operation. Predictive analytics helps identify these risks early on so that the impact is less damaging.
Benefits of Predictive Analytics for Dock Scheduling
Getting a realistic sense of the future and any potential hurdles your dock scheduling operations might face has some serious benefits, including:
Boosted Efficiency
This is perhaps the most important benefit that predictive analytics can have for dock scheduling. Realistic forecasting ensures that companies can be both quicker in their operations and more accurate in their responses which means fewer delays, less risk of facing issues unprepared, and better flow throughout.
Better Budgeting
The financial benefits of using predictive analytics for dock scheduling are two-fold:
- A better sense of future fluctuations allows companies to make more informed budgetary decisions such as how much labor or machinery to have on hand.
- Delays and risks are more easily avoided which helps companies reduce unnecessary or unforeseen expenditures.
Improved Customer Service
More efficient dock scheduling in and of itself means that logistics companies can improve their customer service as they’re less likely to have to log delays and disappoint people. Predictive analytics, however, also empowers companies with more accurate figures on when their customers can expect deliveries. This again limits disappointment and helps companies build a reputation of reliability – a major asset in this industry.
7 Key Metrics for Successful Predictive Dock Scheduling
Predictive dock scheduling does not, unfortunately, happen all on its own. It needs plenty of data in order to build an accurate picture of the future. Here are 7 key metrics to include in a predictive analysis:
-
Past Shipment Data: This is what provides a baseline for patterns in dock usage, seasonal fluctuations, etc., and should include all the details of past shipments such as times, dates, volumes, goods, etc.
-
Dock Utilization Rates: The percentage time that each is dock in use defines the utilization rate which in turn will allow predictive analytics to better illustrate if there are capacity issues.
-
Turnaround Times: How long do trucks take to depart with goods once they’ve arrived? What is the total turnaround time for a pick-up? These are the kind of data points that are vital for predictive analytics as they flag where things are slowing down and, alongside other data, may even reveal patterns on what’s causing delays.
-
Resource Availability: The amount of labor, machinery, and dock space on hand hugely affects dock scheduling accuracy which is why resource availability is such a crucial metric to include for accurate predictions.
-
External Factors: Weather, traffic, and market data all count as external factors worth including in predictive models.
-
The Accuracy of Prior Predictions: If you’ve already run predictive analytics in the past, the rate of accuracy in the predictions versus what actually happened can help refine future forecasting efforts.
-
Customer Feedback: This can be measured using customer surveys or by looking at how many complaints have been made in a given period. These metrics tend to give added color to predictive analytics as they show not just how things are operating on the ground, but the impact on customers.
Look Ahead to Avoid Being Left Behind
The goal of any dock scheduling operation is to keep things running as quickly and smoothly as possible. Little helps in this endeavor more than technology that literally allows companies to see ahead. Predictive analytics offer a window into the future and in doing so can ease dock scheduling costs, boost operational efficiency, and ensure better customer service. In an industry obsessed with timeliness, there is no better technology to assist companies with getting ahead.