Dock Scheduling for Disaster Preparedness and Recovery
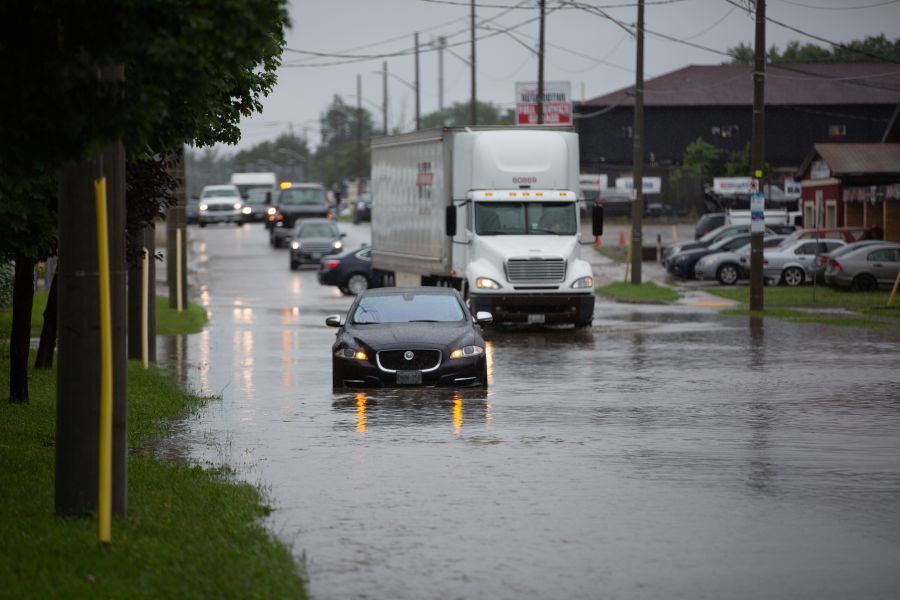
Natural calamities like hurricanes, earthquakes, heavy winters, and floods are becoming worse year after year and have disrupted global supply chains, especially in the U.S. They seriously affect all logistics—maritime, inland, rail, highway, warehousing, and storage.
The latest Post-Tropical Cyclone Beryl in the U.S. is a wake-up call for planning the supply chain for such troublesome occasions. The system spiraled downward until it ultimately stalled because many trucks missed their slots. The worst part is that in 2024, the NOAA expects an 85% likelihood of an above-normal Atlantic hurricane season with 17-25 named storms (the average is 14), 8-13 hurricanes (the average is 7), and 4-7 major hurricanes (the average is just 3).
So, how can the companies be better prepared, given that such events are pretty regular now?
The answer lies in using technology to the advantage of the business. Digitization of logistics can help build visibility and agility of the entire chain for all stakeholders.
For example, robust dock scheduling software can help manage situations where delays are expected, vehicles get stuck for an unknown time, and what will happen next is unclear.
This article covers how digital dock scheduling can help mitigate the effect of disasters on supply chains and keep the company operating with the aid of logistics technologies.
The Impact of Natural Disasters on Supply Chains
The challenges during a natural calamity can be many and really hard to predict. The latest one has been Hurricane Beryl, which struck Texas as a Category 1 hurricane earlier this month (July 2024). It had hit Matagorda with nearly 80 mph winds and caused significant damage.
Like many others, this storm affected over 2.5 million homes, disrupting power, flooding highways, and leaving debris, impacting the companies' logistics operations. Beryl, which initially intensified to a Category 5, the earliest ever in the Atlantic basin, weakened to a tropical depression but caused freight delays.
The economic damage from Beryl is estimated at $28 billion to $32 billion. Not only is this a huge financial loss that will take months and years to recover, but the predictions for the rest of the year 2024 look terrifying. NOAA forecasts an above-normal 2024 Atlantic hurricane season with up to seven major hurricanes, influenced by high sea temperatures and La Nina conditions.
Businesses can't predict these challenges. But they still need to prepare for them. And they can prepare for it with the help of technology. But first, let's take a deeper dive into these challenges:
Shipment delays due to Infrastructure Issues
Adverse weather conditions often significantly disrupt supply chains and lead to delivery delays. A U.S. Department of Transportation and Cambridge Systematics study found that nearly 5% of truck driving hours are affected by weather-related issues like rain, snow, ice, visibility, and wind, resulting in 32 billion lost vehicle hours annually. This costs trucking companies between $2.2 and $3.5 billion.
While each type of weather impacts driving differently, the combination of high winds and flooding from hurricanes causes the most widespread and prolonged delays.
For example, during a flood, key transport routes might become impassable and can completely halt the movement of goods. This affects the timely delivery of in-transit products and creates ripple effects on the deliveries planned for later, causing delays throughout the supply chain.
Loss of Inventory from Warehouse Damages
Warehouses are often vulnerable during natural disasters like cyclones or flooding. Today, the warehouses store the inventory and a lot of tech for the company, like robots, AS/RS systems, conveyor belts, and more.
Storms could damage storage facilities and lost or spoiled inventory might be spoilt. Floods can drown warehouses and ruin stored items inside.
Such inventory losses directly impact a business's ability to meet customer demand and finish orders, causing revenue losses and customer dissatisfaction. Building the warehouse tech ecosystem back also takes weeks, if not months. This affects the customer service for a longer duration.
Increased Operational Costs & Labor Issues
Emergency measures during and after a calamity can increase operational costs and labor issues. Companies may need to expedite shipments to compensate for delays, which come at a premium at such times.
In addition, absenteeism is highest at such times, further delaying recovery. Costs of repairing damaged infrastructure, adding additional resources to manage the crisis, and implementing contingency plans can go out of control.
These unforeseen expenses can strain a company's budget and affect overall profitability for months in the future.
Communication Breakdowns Between Supply Chain Partners
Communication is key to effective supply chain operations. A natural disaster could interrupt communication networks, affecting the flow of communication between supply chain partners such as customers, shippers, and suppliers.
This could complicate and inefficiently cause companies to not communicate about real-time shipment statuses, inventories, or potential operational challenges. This particular miscommunication can worsen delays and operational disruptions.
Dock Scheduling: A Great Tool for Managing Unplanned Events
Dock scheduling is designed to streamline shipment scheduling, ensuring efficient and timely dock operations during normal operations. During disasters, it becomes even more critical to minimize the damages to operations and quickly revert to normalcy.
Modern-day dock scheduling solutions help improve operations' visibility, communication, and predictability.
Many features help improve the reaction in such adverse times, such as:
-
Real-Time Visibility and Communication:
-
Dock scheduling enables real-time tracking of shipments and dock availability.
-
It facilitates instant communication between warehouse managers, carriers, and suppliers to adjust schedules based on current conditions. This helps avoid confusion and keeps everyone on the same page.
-
Dock scheduling can provide a centralized platform for all stakeholders, including warehouse managers, shippers, and carriers, to receive real-time updates on the status of the operations and what to expect next, so that they make informed decisions.
-
-
Automated Rescheduling:
-
Dock Scheduling automatically does the rescheduling if there's a delay or cancellation, keeping dock operations running even during emergencies.
-
Using intelligent rescheduling, the system can react to real-time problems, lowering the downtime and ensuring required supplies reach their desired destination on time.
-
-
Resource Optimization:
-
Post-disaster, resources are often stretched thin. Dock scheduling can optimize available resource allocation, ensuring critical operations continue smoothly.
-
It allocates resources such as dock workers and equipment based on real-time needs, minimizing downtime and ensuring personnel safety.
-
-
Data Analytics:
-
Dock scheduling provides insights into potential vulnerabilities and bottlenecks in the supply chain, allowing for proactive measures to mitigate risks.
-
It can analyze trends from past events' data to predict potential disruptions and create contingency plans. This helps create a Business Continuity Plan (BCP), which makes the supply chain more resilient.
-
-
Integrated with other systems:
-
Dock scheduling integrates with other systems like WMS, TMS, and Planning. Since the dock scheduling gets the latest data on operations, other functions can rely on this data to plan a further course of action. This visibility helps minimize the bullwhip effect within the company operations and helps to recover much faster.
C3 Solutions for More Resilient Supply Chains
C3 Solutions provides customized dock scheduling software for disaster preparedness and recovery.
The FHWA states that poor weather causes 23% of all roadway delays, which can increase with climate change. Extreme weather events like hurricanes present substantial supply chain disruptions that should be controlled with the help of digital solutions.
Companies can offset these events and keep operations running smoothly. C3 Solutions' dock scheduling software helps disaster preparedness and recovery by providing real-time visibility, resource optimization, automated rescheduling, and data-driven decision-making.
Today, businesses require robust dock scheduling strategies to build resilience and be ready for any eventuality.
Learning from situations like Post-Tropical Cyclone Beryl can help companies better prepare for upcoming events and maintain efficient supply chain operations.
Contact C3 Solutions today to learn how we can help to make your supply chain more resilient.