Improving Dock Scheduling in Retail Logistics: Streamlining Processes and Reducing Wait Times
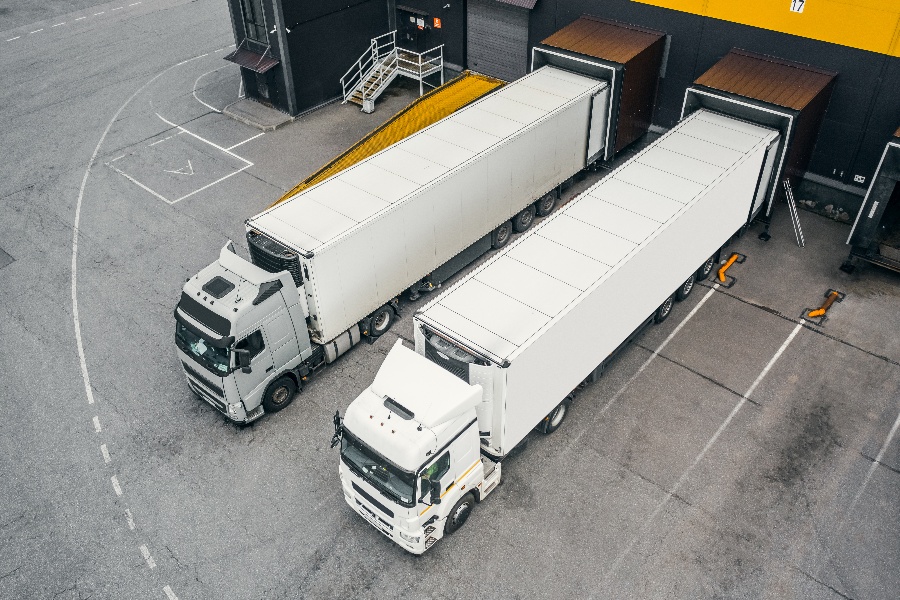
Retailers often work on razor-thin margins, and the shareholders highly appreciate money saved from anywhere as it adds to the company's bottom line. Dock scheduling is a vital element of retail logistics that involves managing the flow of goods in-and-out of distribution centers, warehouses, and even stores. And efficient dock scheduling can be a massive opportunity for optimizing supply chain operations, minimizing costs, and enhancing customer satisfaction for retail businesses.
The dock scheduling process is often riddled with inefficiencies, delays, and bottlenecks, leading to lost revenue, frustrated customers, and wasted resources. This blog aims to provide technical solutions for improving dock scheduling in retail logistics, streamlining processes, and reducing wait times.
What is Dock Scheduling in Retail?
Dock scheduling involves assigning time slots for trucks to pick up or drop off goods at the dock. This process is vital for managing the flow of goods and ensuring that resources are used effectively, but it is often overlooked.
Retailers often find dock scheduling challenging due to many factors, such as manual processes, lack of visibility, and limited resources allocated to this area. Usually, it is not given the importance it deserves for the money it can save, leading to scheduling, loading, and unloading delays. Causes of delays in dock scheduling include:
- Inaccurate or incomplete information to the truckers,
- Unforeseen delays in truck arrivals,
- Unexpected changes in demand, and
- Inefficient resource allocation to the warehouse
These issues can result in wasted resources, missed delivery deadlines, and unhappy customers, and dock scheduling can save much stress in such situations.
Streamlining Dock Scheduling Processes
To address these challenges, retailers can implement modern-day technology solutions to streamline dock scheduling processes. For instance, a real-time dock management system can provide visibility into the status of trucks, dock availability, resource utilization, and other constraints such as capacity and labor. A dock scheduling system can help retailers identify bottlenecks, optimize resource allocation, and prioritize high-value customers.
Automating scheduling and dock appointments can also reduce delays and improve efficiency. Automated systems can prioritize high-volume customers, assign time slots based on availability, and notify drivers in advance of any changes in scheduling. By standardizing dock scheduling processes, retailers can ensure consistency and reduce errors.
For example, a real-time dock management system can help reduce trucks' average time at their distribution centers. The system can provide real-time data on dock availability, allowing drivers to plan their routes more efficiently and reducing wait times. The dock management system can make the modern warehouse even smarter by implementing many features, including:
- Maximizing the use of resources by staggering truck arrivals and departures
- Prioritizing high-volume, high-value customers to reduce their lead times and improve their experience
- Establishing clear communication and updates with carriers to ensure timely arrivals
- Using appointment scheduling to minimize wait times and improve capacity
Another option is using data analytics to identify patterns, trends, and opportunities for optimization. By analyzing data from various sources, retailers can gain insights into the performance of their supply chain, warehousing, and docking and make data-driven decisions for improvement. For example, Amazon uses data analytics to optimize its dock scheduling process by analyzing historic delivery patterns and demand data. A modern-day dock scheduling system can generate this data, which can be used for data analytics to gain such actionable insights.
Benefits of Improved Dock Scheduling
Improved dock scheduling can provide several benefits for retailers, including:
- Increased efficiency
- Reduced wait times
- Improved customer satisfaction
- Provide great ROI on the investment
- Better resource utilization
- Reduce demurrage fees
- Optimize labor costs, and
- Better decision-making based on data analytics
By optimizing the dock scheduling process, retailers can improve their bottom line and enhance their competitive advantage.
Want to learn how to maximize your Yard Management and Dock Scheduling Investment ? Download this Comprehensive ROI Overview to Help Build Your Case.
Conclusion
Improved dock scheduling can significantly benefit retailers, such as reduced operating costs and better resource utilization. By making data-driven decisions and optimizing the scheduling process, retailers can enhance their competitive advantage and improve their bottom line. Retailers must calculate their ROI before investing in a system, and an efficient system like Dock Scheduling by C3 can give excellent results.
In conclusion, retailers must prioritize efficient dock scheduling as part of their supply chain management strategy. With the help of an effective solution, retailers can reduce wait times and improve resource utilization. Retailers can enhance customer satisfaction, reduce costs, and boost their supply chain performance. With continued investments in technology and process improvements, retailers can stay ahead of the curve and succeed in the dynamic retail landscape.