The Future of Contactless Delivery: Integrating AI with Dock Scheduling
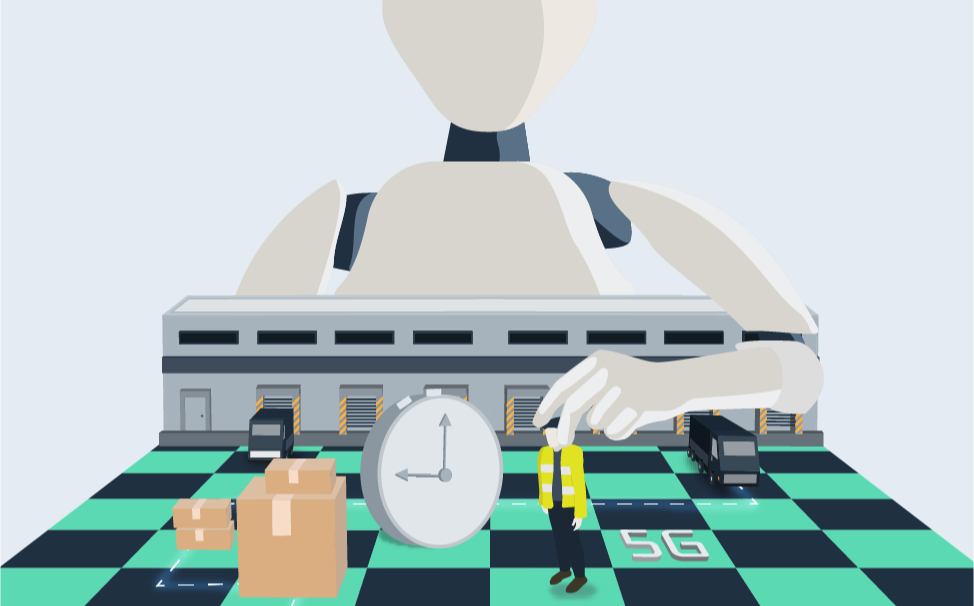
Dock scheduling has successfully added significant value to the supply chains and, hence, is seeing a lot of acceptance.
The market for dock scheduling software is projected to expand at an annual growth rate of 11.34% from 2024 to 2029, with its value anticipated to approach US$ 10.20 billion by the end of 2029.
Presently, the US holds 32% of the worldwide market. In the European Union, Germany is expected to grow at approximately 12.09% CAGR during this period.
Integrating AI will be a watershed moment to enable the next level of growth in dock scheduling.
The fast-evolving concept of AI-powered contactless deliveries sets the stage for transforming the logistics and supply chain sector.
As we venture deeper into the digital era, the emphasis on automation, enhancing operational efficiency, and elevating customer satisfaction has reached unprecedented levels.
The fusion of AI with dock scheduling emerges as a critical strategy to realize the vision of seamless, contactless delivery services, illustrating a significant leap toward redefining the logistics and supply chain landscape.
The Rise of AI in Dock Scheduling
AI plays a crucial role in reshaping dock scheduling and delivery processes.
With its manual inputs, delays, and inaccuracies, traditional dock scheduling is all set for an AI-powered makeover.
AI can crunch massive amounts of information, anticipate scheduling conflicts, and improve real-time delivery routes to ensure the right load gets to the right dock at the right time.
Aside from crunching data, integrating AI into delivery processes enhances operational efficiency in various ways.
-
Predictive Scheduling: The core of predictive scheduling is AI-based algorithms that can predict peak times and possible delays, helping optimize slot scheduling for effective usage of dock capacity. Such predictive scheduling can use analytics and machine learning to assign docking times automatically to ensure deliveries are distributed evenly during the day. This helps determine ideal routes based on scheduling, thereby, improving loading and unloading operations. This ensures a simplified supply chain from warehouses to the final delivery areas without human judgment, reducing manual communication and boosting efficiency.
-
Connecting to Autonomous Vehicles: Contactless deliveries are expected to be the norm with the advent of autonomous vehicles like self-driving trucks. AI helps manage the integration of these vehicles into the dock scheduling process. AI-enabled dock scheduling systems can schedule exact arrival times, establish specific loading areas, and manage cargo movement without human input by directly communicating with autonomous vehicles. The same applies to yard-based systems, such as automated yard trucks and automated storage & retrieval systems (AS/RS).
-
Real-Time Adjustments: Real-time adaptability is a crucial feature of contactless deliveries. AI elevates it by continually monitoring delivery times and situations using information from several sources, such as traffic patterns, weather, and functional capacities, to optimize delivery times. AI can optimize real-time schedules because of unexpected delays, reducing downtime and enhancing flexibility.
-
Automated Communication: AI-enabled dock scheduling systems inform every stakeholder in the end-to-end value chain — from warehouse managers to drivers and clients — allowing transparency while minimizing manual updates and human dependency.
Improving Operational Efficiency
The integration of AI within dock scheduling systems is transformative to enhance in-house operational efficiency.
By leveraging AI, businesses can streamline their internal processes, from scheduling to real-time monitoring, ensuring a seamless flow of operations within the docks and warehouses.
This not only optimizes the utilization of resources but also sets the stage for a more agile and responsive operational framework.
-
Less Waiting Times: AI decreases driver wait times at docks by optimizing scheduling, lowering idle time, and increasing delivery throughput. For example, AI with text recognition can read the license plates of trucks when they arrive and then guide them to the correct dock.
-
Lower Operating Costs: AI is being used to automate tasks in the docks and decrease downtime. Another interesting application is that, with cameras linked to AI software, the system monitors dock activity. It identifies anomalies or patterns, like 30 minutes without movement, and notifies staff to rectify delays. This enables drivers to leave on time, enabling deliveries or pick-ups to be completed quicker. This leads to effective use of resources, lowering labor, maintenance, and fuel expenses in operating costs.
-
Improved Resource Allocation: Beyond simplifying operations at the docks, AI's impact is felt across the warehouse, significantly improving efficiency and workflow. AI enables warehouses to allocate resources better, from dock employees to equipment loads, based on scheduled delivery volume and type.
Improving Customer Satisfaction
On the flip side, the application of AI extends beyond the confines of operational efficiency, directly influencing the external, consumer-facing aspects of the business.
By harnessing the power of AI in dock scheduling and logistics, companies are able to offer faster, more reliable, and highly personalized delivery experiences to their customers.
This not only enhances customer satisfaction but also fosters a sense of trust and loyalty towards the brand.
-
Faster & Accurate Deliveries: AI is a vital enabler for route planning & delivery time reduction. This technology can predict arrival times and enable warehouses to ready docks for incoming shipments. Optimized scheduling results in decreased loading and unloading times, leading to quicker delivery and happier customers.
-
Improved Transparency: Trust & loyalty-based real-time tracking and automated notifications keep customers informed of deliveries at all times. Automated communication in case of unexpected delays or issues helps keep the customer updated and builds trust.
-
Customized Delivery Experiences: AI can provide flexible delivery times and personalized assistance based on consumer preferences. Key accounts can be given special treatment with such privileges attached and reserved for them. Such premium support will make them feel valued and work together as a partner.
Overcoming Problems with AI
While AI for dock scheduling has numerous advantages, it also has drawbacks that must be planned for and monitored:
-
Data Privacy & Security: Data security for information gathered and analyzed by AI systems is crucial for protecting company and customer information.
-
Integration with Existing Systems: AI solutions should be integrated with the existing systems, like Enterprise Resource Planning (ERP), Warehouse Management Systems (WMS), Transportation Management Systems (TMS), and other reporting and analytics frameworks. An integrated system will unlock the real power of using AI in dock scheduling.
-
Adoption & Training: When using AI, building certain capabilities in-house will ensure that the systems are well-managed and the costs of managing them are in check. This requires a cultural change of promoting AI systems and training staff members to use AI capabilities to gain the maximum value out of it.
The Road Ahead
The potential future of contactless delivery with AI integrating with dock scheduling is bright, and many companies have already placed big bets on it.
From autonomous vehicles sync with dock schedules to AI-powered real-time adjustments, we expect more advanced AI applications in logistics as technology evolves.
AI adoption in dock scheduling is driving new benchmarks in efficiency, safety, and customer experience for logistics businesses.
With businesses such as C3 Solutions leading the charge, the promise of AI-powered delivery methods is becoming a reality, allowing quicker, smarter, and contactless deliveries.
C3 Solutions: Leading the Way for AI Integration
C3 Solutions is a pioneer in building AI for dock scheduling, producing solutions that meet the demands of contemporary logistics:
C3 Reservations: A dock scheduling solution that automates scheduling and offers predictive analytics and real-time adjustments for dock utilization and delivery performance.
C3 Yard: A cloud-based complete yard management solution for visibility, efficiency, and safety in the yard. An online suite of tools that empowers yard managers by providing visibility on both yard assets and shipments, increasing gate throughput, and reducing detention costs.
As we begin a digital transformation of the logistics business, AI combined with dock scheduling is a genuine innovation that takes contactless delivery to brand-new heights.
The potential future of contactless delivery is huge, with opportunities to enhance operational efficiency, digital integration, and challenges to customer experience.
With companies like C3 Solutions leading the way, AI in dock scheduling is shaping the future — transforming how we view it.