Optimizing Yard Management for Cold Storage Facilities
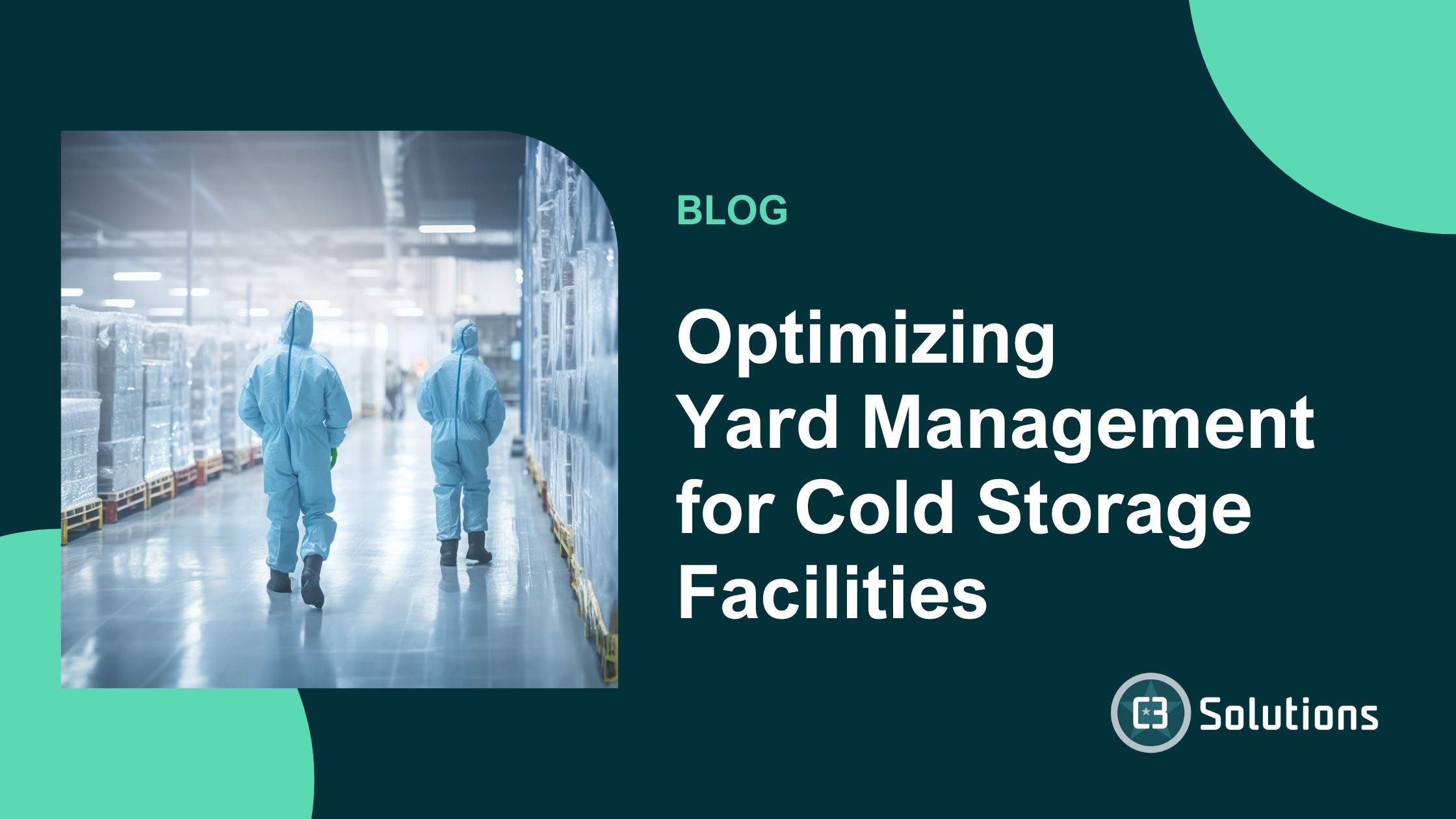
In the ever-evolving world of supply chain management, cold storage facilities present unique challenges that demand precision, efficiency, and technological integration. Yard management, particularly in cold storage environments, is more than just organizing trailers and trucks—it’s about protecting temperature-sensitive goods, ensuring timely deliveries, and mitigating costly errors. In this blog, we will delve into the essentials of yard management for cold storage facilities, discussing the challenges faced, the best practices to overcome them, and how technology can be a game-changer.
The Complexities of Cold Storage Yard Management
Cold storage facilities, unlike standard warehouses, handle perishable goods like food, pharmaceuticals, and chemicals, where even slight temperature fluctuations can lead to spoilage or contamination. This adds layers of complexity to yard management:
-
Temperature-Sensitive Products: The importance of maintaining strict temperature control in cold storage makes it critical to minimize the time trailers spend outside the warehouse or in the yard. Prolonged exposure to ambient temperatures can compromise product quality, leading to significant financial loss.
-
Regulatory Compliance: Cold storage facilities must adhere to stringent industry standards and regulations, such as the FDA’s Food Safety Modernization Act (FSMA). Yard operations must account for these requirements, ensuring that transportation timelines, sanitation, and handling procedures meet the necessary guidelines.
-
High-Volume Traffic: Cold storage facilities often experience high traffic volume due to demand for frozen and refrigerated goods. This creates congestion in the yard, increases wait times, and complicates the scheduling of inbound and outbound vehicles.
-
Limited Dock Availability: Many cold storage facilities have a limited number of temperature-controlled loading docks. With limited space, prioritizing which trucks to load and unload first is crucial to prevent spoilage and keep operations running smoothly.
-
Safety Concerns: Cold storage yards can be hazardous environments. Icy or wet conditions increase the risk of accidents, while the constant movement of trucks and trailers adds another layer of complexity. These factors make safety a top priority when managing the yard.
Best Practices for Effective Yard Management in Cold Storage Facilities
To overcome these challenges, cold storage facilities must adopt best practices in yard management. Here are some of the key strategies to ensure smooth and efficient operations:
1. Prioritize Time-Sensitive Loads
Given the temperature-sensitive nature of the goods in cold storage, facilities must prioritize time-sensitive loads. This means focusing on minimizing dwell times for trucks carrying perishable items and coordinating dock schedules to ensure that trailers don’t remain in non-refrigerated areas longer than necessary. This requires a high level of coordination between the dock scheduling team and yard managers.
Advanced Dock Scheduling Software (DSS), like the solutions offered by C3 Solutions, can help streamline this process by ensuring that trucks are assigned to docks efficiently based on their load requirements. This technology minimizes the idle time of refrigerated trailers, reducing the risk of temperature breaches.
2. Implement Real-Time Yard Visibility
One of the most effective ways to optimize yard operations is through real-time visibility. Cold storage facilities can benefit immensely from Yard Management Systems (YMS) that offer real-time tracking of trailers, trucks, and other assets. Knowing where each trailer is located and how long it’s been there allows managers to quickly make decisions, whether it’s moving a trailer to a temperature-controlled dock or ensuring that a load is dispatched on time.
Real-time visibility also ensures that trucks are moving through the yard efficiently, reducing bottlenecks and wait times. For cold storage, this level of visibility is essential to ensure products maintain the proper temperature throughout their stay on-site.
3. Optimize Dock and Trailer Management
Given the limited availability of refrigerated docks, it’s essential to optimize how you use this space. Cold storage facilities should leverage YMS tools to automate the assignment of trailers to docks based on priority, load type, and temperature requirements. YMS technology can track which docks are in use and schedule future arrivals accordingly.
Additionally, using automated gate systems can improve efficiency. For example, incorporating automated vehicle access can significantly reduce check-in and check-out times for trucks, allowing for quicker turnaround and reduced congestion.
4. Plan for Seasonal Demand Fluctuations
Cold storage facilities often see sharp spikes in demand during certain times of the year—think holiday seasons or harvest periods when food supply chains are at their peak. Preparing for these fluctuations is essential to avoid gridlock in the yard.
By analyzing historical data and anticipating peak seasons, facilities can ensure they have the right resources in place—whether that means increasing staff, optimizing dock schedules, or leasing additional trailers. Having contingency plans for managing yard space during busy periods can help avoid disruptions and ensure that product quality is maintained.
5. Enhance Safety Protocols
Safety in a cold storage yard is non-negotiable. Facilities should implement strict safety protocols, especially during adverse weather conditions that can make driving in the yard hazardous. This includes ensuring that drivers are well-trained and that equipment like forklifts and trucks are properly maintained to avoid accidents.
YMS solutions can also contribute to safety by reducing the need for manual interactions between yard workers and trucks. For example, real-time trailer tracking can automate many tasks that would otherwise require human intervention, decreasing the chances of accidents.
The Role of Technology in Transforming Cold Storage Yard Management
The introduction of advanced yard management technology has revolutionized the way cold storage facilities operate. Yard Management Systems (YMS), automated gate systems, and Dock Scheduling Software (DSS) can work in unison to tackle the key challenges of cold storage yard management. Let’s look at how these technologies can improve efficiency, safety, and product quality.
1. Yard Management Systems (YMS)
A Yard Management System provides end-to-end visibility of the yard’s operations, allowing managers to track and manage trailer movements in real-time. For cold storage facilities, this is invaluable because it reduces dwell time, ensures quick turnaround, and prevents trailers from being parked in unsuitable areas.
A YMS can also optimize trailer-to-dock assignments based on load type, allowing for better utilization of refrigerated docks and ensuring that temperature-sensitive products are handled with care.
2. Dock Scheduling Software (DSS)
Dock Scheduling Software helps streamline the scheduling process by automating appointment bookings and coordinating the arrival and departure of trucks. This reduces wait times and ensures that docks are being used as efficiently as possible. For cold storage facilities, DSS can be a game-changer by prioritizing loads based on temperature sensitivity, ensuring that trailers spend as little time as possible outside the controlled environment.
3. Automated Vehicle Access Systems
Cold storage facilities can also benefit from automated gate systems that track and manage vehicles entering and leaving the yard. These systems can drastically reduce wait times at gates, helping to avoid bottlenecks and keeping yard traffic flowing smoothly. When combined with real-time visibility tools, automated gate systems can provide a more comprehensive view of yard operations, enhancing overall efficiency.
Conclusion
Cold storage facilities face a unique set of challenges when it comes to yard management. From the need for temperature control to high traffic volumes and regulatory requirements, effective yard management is crucial for maintaining product integrity and ensuring smooth operations.
By adopting best practices such as prioritizing time-sensitive loads, implementing real-time visibility, and leveraging advanced technologies like Yard Management Systems and Dock Scheduling Software, cold storage facilities can overcome these challenges and improve their operational efficiency. The result? Reduced spoilage, better compliance, and a more organized, efficient yard.
In today’s fast-paced, temperature-sensitive supply chains, investing in the right yard management solutions isn’t just an option—it’s a necessity for staying competitive and maintaining product quality.