Efficient Dock Scheduling will Maximize Investments in Demand Sensing
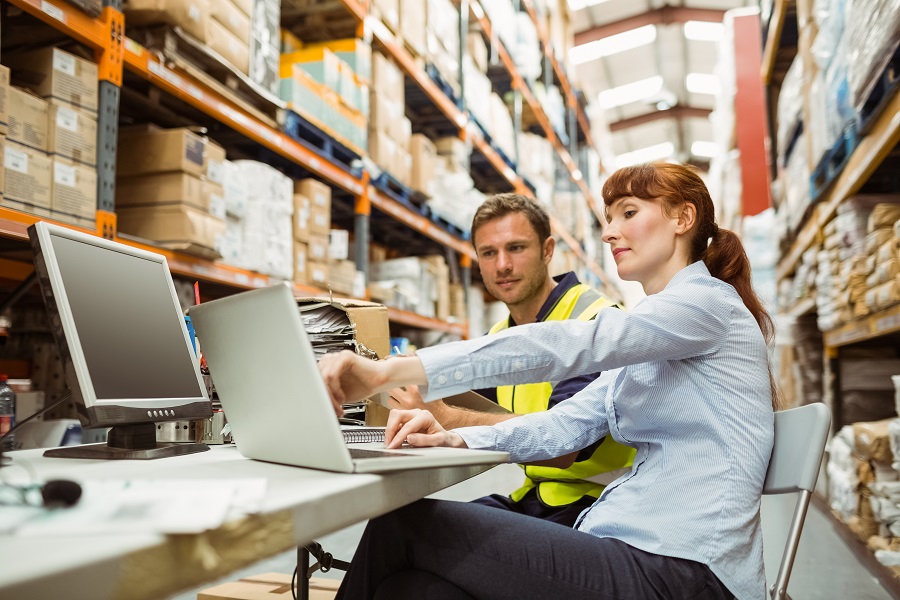
Demand sensing relies on the automation of analytics, machine learning and real-time information to improve forecasting for a given facility, such as a retailer or warehouse. Unlike traditional forecasting, its advantages lie in adjusting the forecast around the clock and enabling continuous improvement in inventory planning. Unfortunately, failure to realize its benefits remains. Supply chain professionals need to understand why and how to overcome such challenges through efficiency in dock scheduling.
Hurdles of Demand Sensing
Since demand sensing is a process affecting the flow of inbound freight, limited visibility remains its most significant hurdle. Thus, the hurdles of visibility are a direct influence on the value of demand sensing. Challenges with visibility include:
- Limited access to data.
- Inability to analyze data or access systems remotely.
- Poor integration, if any, of systems.
- Lack of inventory visibility.
- Poor use of customer data.
- Failure to future-proof supply chains during times of crisis.
Take added note of the final challenge; limited visibility results in low ability to respond to disruption and uncertainty. The problem only grows worse as product lifecycles shrink.
Demand Sensing Relies on Efficiency in Dock Scheduling
A successful demand sensing program leverages both internal and external data sources to derive the most accurate, near-future model possible. As explained by Logility, “some appropriate data sources for collecting data in a demand sensing program include sales orders, campaigns and promotions, new production introductions, POS data from the field, economic trends, competitive tactics, consumer behavioral changes, and weather-related information.” Collecting data across the spectrum ensures the most accurate forecast, but it holds added value beyond simple inventory management.
For example, demand sensing improves procurement processes, helping your organization realize when reordering is necessary for advancement. Moreover, such information is valuable to suppliers. Since suppliers have long held power in procurement, demand sensing provides a means to manage inbound freight better, yielding benefits for both parts, explains Logiwa.
How to Increase Dock Management & Efficiency
The steps to increase efficiency in dock scheduling and management lie in gaining control over your facility’s inbound and outbound processes. A few tips for improving efficiency include:
- Consolidate inbound freight deliveries into the largest possible load. Freight consolidation is an excellent venue for improving dock efficiency. According to MH&L Magazine, the time needed to unload 10-14 LTL shipments is more than the time required to unload a single FT. Efficiency through consolidation also means less time managing gate and yard traffic too.
- Implement dynamic vendor compliance standards, such as a dynamic inbound freight routing guide. It’s more than just sorting the good shipments from the bad and managing chargebacks. It’s about collaborating with your vendors and carriers to identify where the faults lie and finding solutions. Your business can achieve this goal by investing in efficient monitoring, reporting and communication tools to identify problematic areas.
- Integrate supply chain systems with the dock scheduling software. Integration with the dock scheduling software helps to avoid overlooked issues that may result in disruptions. Moreover, integration allows for more access and application of data for analytics that power demand sensing.
- Negotiate with carriers to secure better rates and status, such as shipper-of-choice status, which may open more delivery windows for use by your organization. Better rates may also amount to added benefits, such as carrier-provided consolidation programs and more.
Reap the Value of Demand Sensing and Better Dock Management Now
Demand sensing is analytics-based, real-time forecasting. But like all forecasting capabilities, it is only as valuable as the ability to change operations and respond to the issues at hand. In this case, demand sensing means your dock needs to have the flexibility to scale operations and avoid disruptions. Fortunately, implementing a dock scheduling software that enables efficiency in dock scheduling will go a long way in truly maximizing the value of demand sensing. Find out more about how your organization can take advantage of such software by scheduling a demo with C3 Solutions online today.