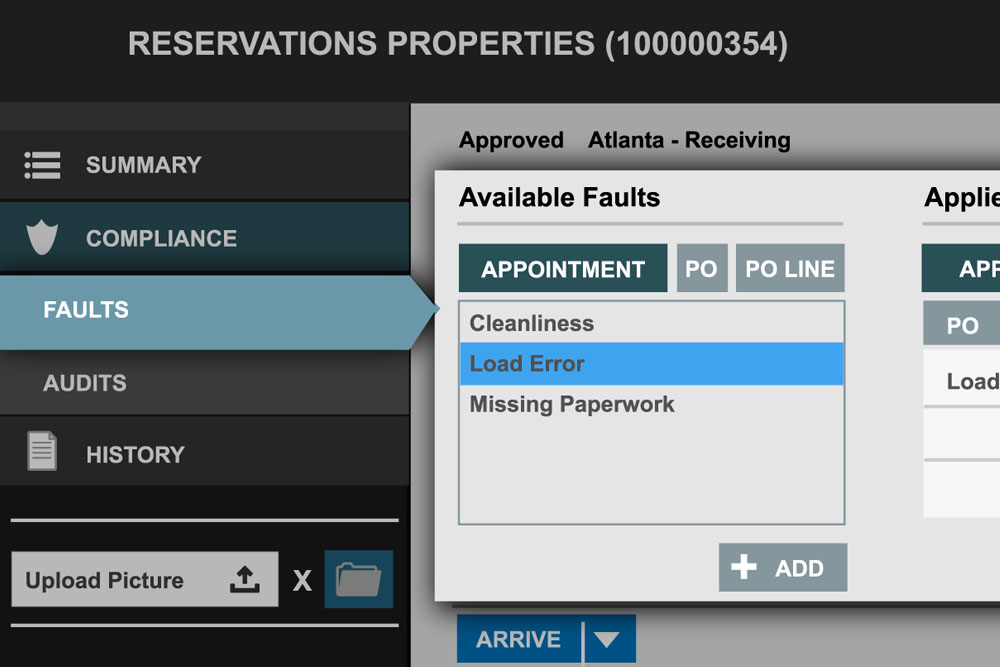
What to include in the receiving audit questionnaire
For their own trailers, they wanted to keep track of cleanliness, damages, weight requirements, trailer identification and whether the pallets were safely stacked. Once these trailers were at the store, it was now the store receiving team’s responsibility to confirm whether the load met their expectations, and that the freight arrived in good condition and without product damage.
A similar audit process can be easily implemented for third-party carriers or vendors. The questions and factors you wish to measure should reflect your business priorities; which may evolve regularly.
The automation solution
In the course of implementing a web-based dock scheduling system, this retailer seized the opportunity to implement an integrated compliance module. Since the dock scheduling application already has the appointment and purchase order information, it is easy to link a receiving audit module directly to it.
When the appointed trailer arrives on site the receiving clerk cannot release the trailer without completing the receiving questionnaire online. In a matter of seconds, the person can upload pictures, include comments and quickly complete the form.
The application then automatically compiles and reports on the audit, rendering it accessible to the business and its partners in real-time, either by email or via their web portal access. In other words, the receiving audit occurs between the arrival and departure times without slowing the unloading time and without burdening your compliance/quality department. That’s a win-win solution!
If you'd like to have more information on all the options available to improve your dock operations, you can reach out to our industry experts team.