How To Deal With Carrier Late Arrivals
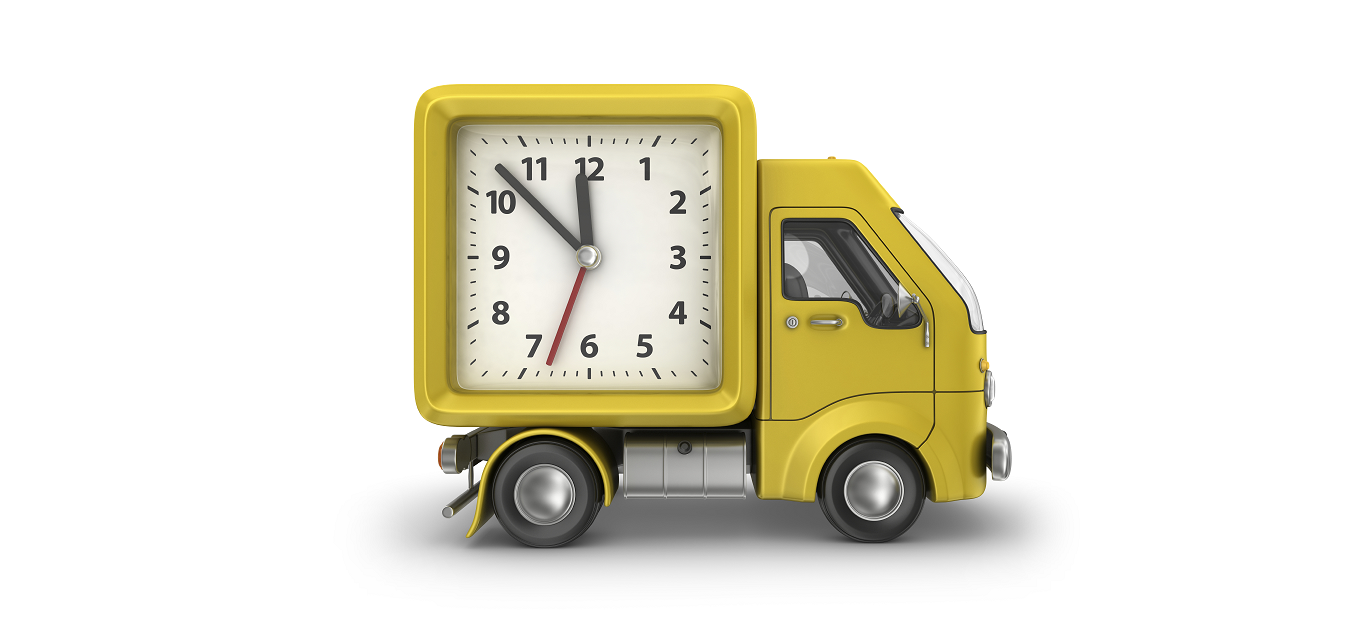
Managing carrier arrivals is crucial to efficient warehouse operations, especially when it comes to dock scheduling. However, late arrivals can disrupt even the best-laid plans. We hosted a webinar where two experienced warehouse managers discussed how they handled late arrivals before and after implementing dock scheduling software. A common question from the audience was: How does your warehouse manage late arrivals?
Given the frequency of this issue in warehouse environments, we wanted to share key insights from the webinar and feedback we regularly gather from clients using appointment scheduling software.
Establishing a Clear Policy for Late Arrivals
A consistent theme from the webinar was the importance of having a well-defined company policy. Clear rules around scheduling appointments and what constitutes a “late arrival” are essential. This policy helps streamline operations and prevents misunderstandings between warehouse teams and carriers.
Most companies define a late arrival as 30 minutes past the scheduled time. From our industry experience, grace periods generally range between 15 to 30 minutes. This clarity ensures that warehouse automation processes run smoothly and minimizes delays in load management.
Managing Late Arrivals: Best Practices
When a carrier is late, how do you handle the situation? The approach depends on several factors, including the priority of the load, day of the week, and time of day. The two warehouse managers from the webinar agreed that fitting the late carrier into the next available slot was often the best solution. However, this depends on operational flexibility and how critical the load is.
Both managers also stressed that scheduling software plays a key role in managing late arrivals. One manager implements a $90/hour overtime charge if unloading must be done after regular hours. This small penalty incentivizes carriers to arrive on time. Another manager opts to reschedule late arrivals for the next day, especially if their warehouse automation systems do not allow for after-hours unloading.
Early Arrivals, No-Shows, and Very Late Loads
While late arrivals present challenges, early arrivals and no-shows are also significant issues that affect dock scheduling.
Handling Early Arrivals
Early arrivals may seem like a minor issue, but they can disrupt warehouse workflows. Warehouse personnel typically have two options:
-
Ask the driver to return at their scheduled time.
-
Place the driver on a standby list to fill any gaps created by late arrivals or cancellations.
To effectively manage early arrivals, some warehouses create a standby system using appointment scheduling software to monitor waiting drivers. This ensures that early arrivals don’t disrupt dock activities, particularly in operations with cross-docking processes, where efficient flow is crucial.
Managing Very Late Loads
When a load is extremely late, it disrupts the entire load management schedule. The previously reserved time slot becomes available, and without a proper scheduling app or dock scheduling software, it’s easy for these gaps to go unfilled. Creating a standby list is a practical solution for filling empty slots, helping to minimize productivity loss.
No-Shows: Defining and Handling
A “no-show” can severely impact scheduling appointments. Warehouses need to define what constitutes a no-show and implement clear penalties. Some companies require carriers to reschedule missed loads, while others impose penalties based on hours lost. Your appointment scheduling software can help track these occurrences and streamline how your warehouse handles no-shows.
Reporting: The Backbone of Accountability
To enforce any policies regarding late or no-show arrivals, you need solid reporting. Manual tracking through spreadsheets is labor-intensive and often inaccurate. Warehouse automation tools like dock scheduling software make tracking easier, allowing for real-time data collection and reporting.
These tools provide comprehensive reporting on appointment adherence, late arrivals, and no-shows, enabling you to make data-driven decisions. When using appointment scheduling software, you can confidently enforce your policies, knowing that you have the data to back them up.
Conclusion
Timely shipments are essential for efficient warehouse operations, but late arrivals, early arrivals, and no-shows are inevitable. By implementing a clear policy, using the right dock scheduling software, and creating backup systems for early arrivals and standby drivers, warehouses can minimize disruptions and maintain efficiency.
To hear more insights from warehouse managers on managing carrier arrivals, listen to our webinar or download the transcript. And if you're looking for a solution to streamline your dock scheduling and improve overall warehouse efficiency, talk to an industry expert today about how C3 Solutions' dock scheduling software can help.