The Advantages of YMS Automation
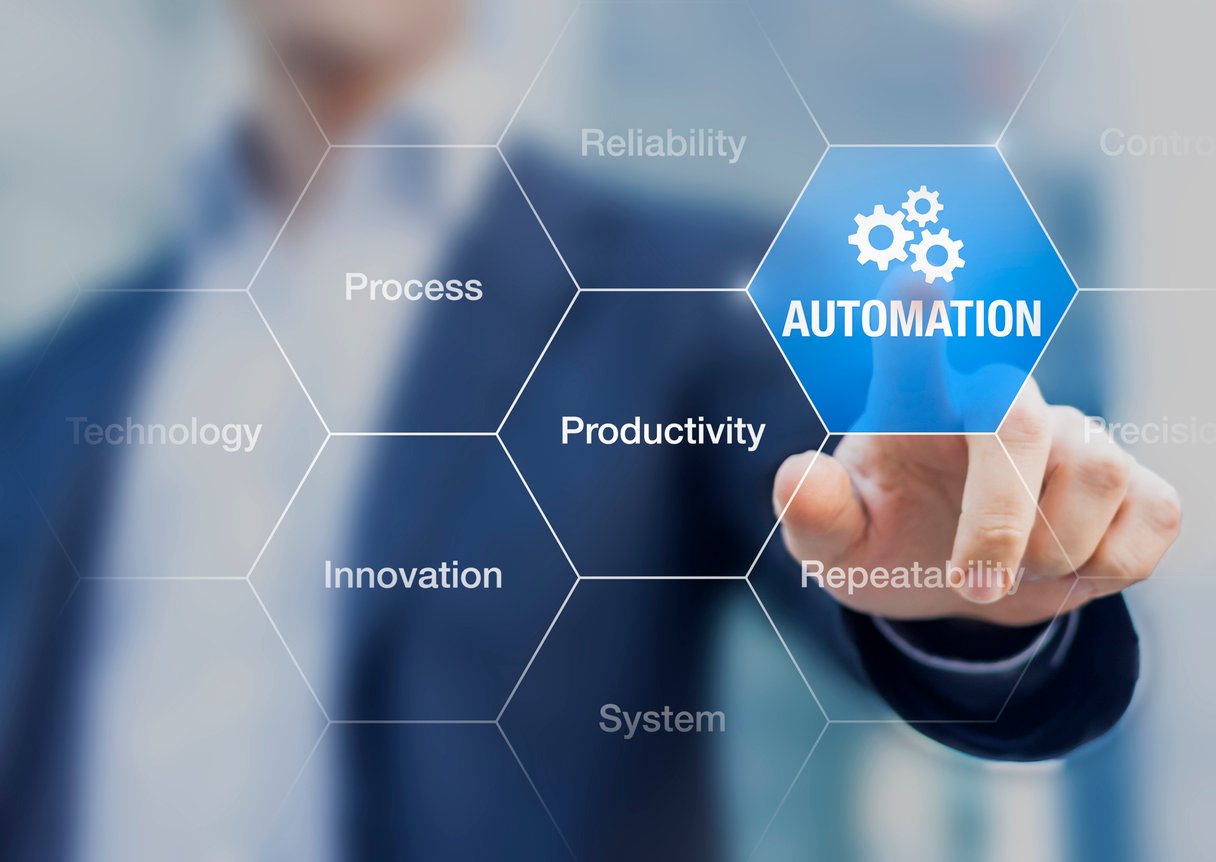
As organizations around the world seek to increase the use of automation and integrate artificial intelligence (AI) into their production facilities, there is a clear pursuit of replacing repetitive tasks performed by people, with computerization and robotics.
At the start of each year during my time working as the head of several large UK parcel distribution facilities, I would regularly be confronted with a seemingly unassailable challenge: “How do I remove costs while maintaining productivity”. No doubt a common conundrum for department leads and VP’s across the sector. Moreover, how can I ensure that my team and I do not strip away quality during the streamlining process? What seems like a contradiction in terms, can cause you to look differently at the problem.
Any task, that follows a step-process, has standardized data requirements and defined outcomes and can be automated, by using the right software or AI – if this sounds abstract, I will go into detail about how the inbound gatehouse process in a distribution facility works. Not only can automation successfully replicate the manual process, in almost all cases it will improve data capture, speed of site-access, shipment throughput and security.
The Manual Gatehouse
Whether looking at a large facility with thousands of vehicle arrivals per day, or a small site that sees far less activity, the security gatehouse is a common standard for securing access and egress. The process tends to track the following stages:
-
The Driver arrives at the gatehouse and confirms their credentials to the gate-guard (usually both verbally and with paperwork).
-
The gate-guard then enters the details into the computer terminal (name, licence plate, trailer number, route/customer name, the volume of trailer fill etc). This process is often time-consuming and fraught with the possibility of admin/typing errors.
-
If a parking space or dock door is not visible or known by the gate-guard, the gate-guard must call an operational colleague to find out where to send this vehicle.
-
Once the desired location has been ascertained, this is verbally communicated by the gate-guard to the driver (who hopefully knows the site already and can swiftly drive to the destination and park effectively).
-
If the site does not have a Dock Scheduling or Yard Management System, there is every chance the space/door will be occupied. This means the driver will be delayed further while they search for a new spot, and the operation will have to search to find the new trailer/vehicle when it is required in the operation.
In the manual process, you are reliant on the experience, speed and efficacy of the gate-guard and drivers alike. If either individual is unfamiliar with the process it will add further time delays for the vehicle and its contents, and inadvertently cause delays for every other vehicle waiting behind it. Any time the gate-guard needs to leave their post (training, meetings, breaks et al), their gate is rendered inactive or will have to be covered by another team member, this can be made more difficult to cover on low volume days when labour is scarce.
The Automated Gatehouse
The backbone to any automation in a gatehouse or goods-in environment is a fully integrated Dock Scheduling or Yard Management system. These systems help operations govern the step-processes by replicating manual protocol and harnessing speed and security.
A driver who would normally have to hand over paperwork to a gate-guard can simply enter the site by scanning a barcode, QR code or entering a unique number to a fixed gate kiosk; all of which the driver has received from the customer when they were picking up the vehicle/load or at the start of their shift from a transport clerk who has access to the DSS or YMS portal. Scanning of driver access cards can also beef up the security element at the gate without compromising safety or time.
Not only does this remove the need for paperwork, (something which helps all businesses to improve their Green credentials), but it also speeds up site-access due to the removal of lengthy data entry via the gate-guard.
Following the driver check-in process, the DSS or YMS will then pinpoint and optimize a dock door or parking bay for that arrival – and display instantly all relevant data to the driver via the screen or kiosk at the gate – again removing the need for phone-calls, interaction or delay.
The driver can also receive a printed gate pass at this point. This gives him the task instructions in physical form, and could even have the details of their outbound job; allowing them to efficiently leave the site without having to report to a transport clerk.
Not only is the driver getting on site more quickly, but the system is capturing all the relevant details and making it visible to the security or management teams.
When I transitioned to C3 Yard YMS and automated gatehouses in the UK parcel facilities, my team found a reduction of gate entry time by 50%, reduction of queuing to almost zero and data errors became a thing of the past. Time from gate to door also significantly decreased as drivers had a far clearer idea of where they were to go next.
This goes to show that you can remove costs and be more productive whilst improving quality and security - this benefits not only the bottom line, but it also allows your people to focus on leadership & management instead of repetitive tasks, engaging people with customers and their colleagues, making their jobs easier and less fraught with stress.