Gestion des rendez-vous aux quais : Une exigence pour les détaillants qui doublent leurs efforts en matière de WMS et de WES
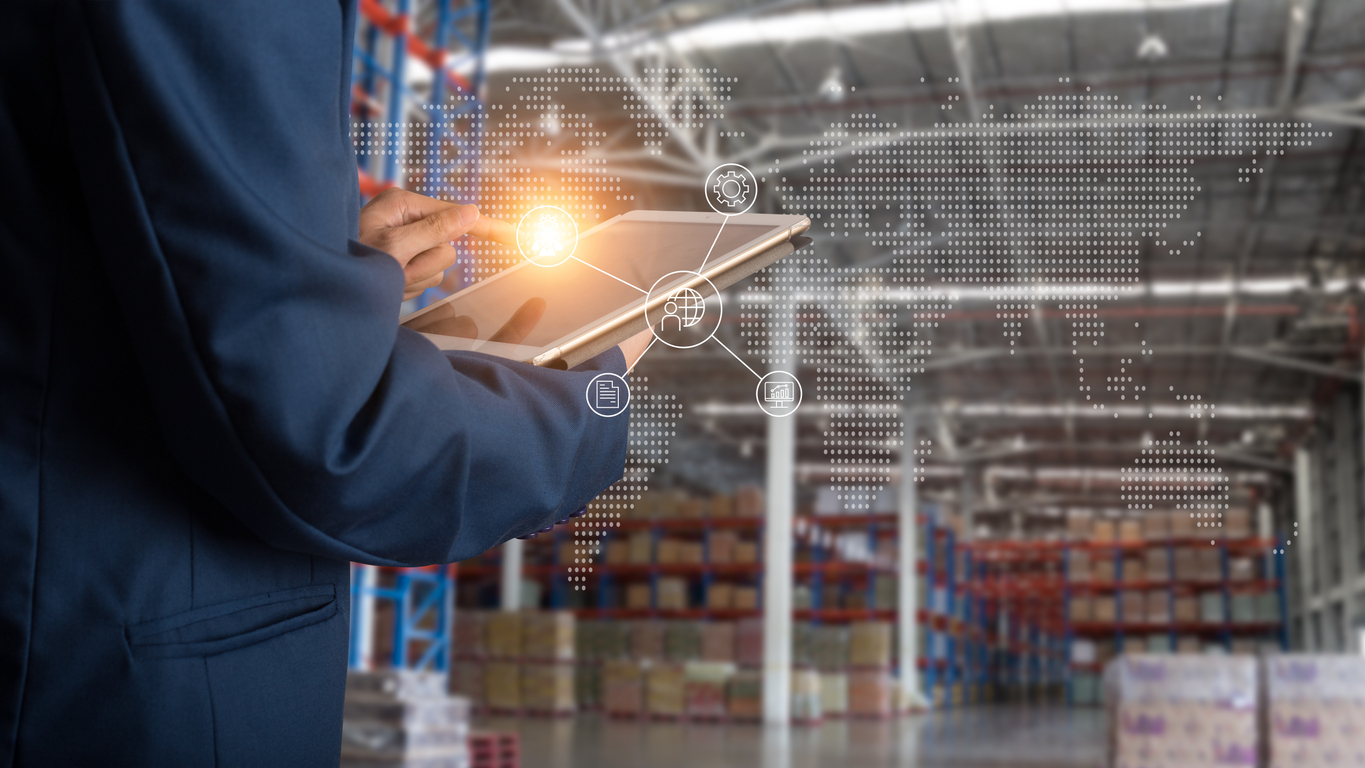
Supply chains across the globe need more efficiency to survive.
The opportunities to grow fulfillment and improve the flow of inbound and outbound freight depend on multiple factors. Items need efficient unloading and comprehensive, digital put-away processes.
Outbound shipments require optimization to minimize touches and avoid unnecessary dock delays. The complexity requirements forced companies to adopt a warehouse management system (WMS) or even a warehouse execution system (WES). Both systems, as well as hybrid versions, are rapidly reshaping the standards of dock and logistics management, and the trend is expected to continue. According to PRNewswire, “The warehouse management system market is expected to reach USD 4.82 billion by 2024 from USD 2.06 billion in 2018, at a CAGR of 15.2% from 2018 to 2024.” As a result, more companies will turn to dock scheduling systems to maximize value. But first, supply chain professionals need to understand the challenges of managing the dock without connected systems, how a scheduling system enhances WES and WMS value, and a few tips to maximize ROI.
Challenges of WES and WMS Without Connected Dock Management
Failure to connect dock management resources with the WES and WMS effectively leaves money on the table. Unfortunately, the challenges only grow more severe with time and added supply chain interactions. Such challenges include:
★ The facility is currently being operated in an old-fashioned, manual way.
★ No form or fashion of moving forward.
★ Efficiency is and will continue suffering.
★ Work overload on labour, resulting in more overtime hours and less profitability.
★ The constant flow of goods and products coming in and going out may be extremely overwhelming.
★ Chances of forgetting important needs and details are highly likely.
★ Reports may be hindered or lost entirely due to inefficiency.
★ Last-minute surprises and their result in a rough change of pace.
★ A constant lineup of trucks in the yard, resulting in higher dwell time and risk for detention charges.
★ Truck drivers are continually in your ear about waiting times.
★ Safety can be compromised.
★ Maintenance is most likely skipped due to rushing.
Dock Scheduling Systems Are Essential to WES and WMS Replenishment and Inventory Management
The WMS is more than just an inventory control system. It provides a means to manage the full flow of merchandise, people, equipment, and orders in the warehouse. The same can be said about the dock scheduling software. Then again, dock scheduling software does more than just appointment direction. Once implemented into your facility, the system becomes a smart schedule. It intuitively adds the necessary steps to select and apply critical WMS and WES functions without compromising dock safety and efficiency. Multitasking on different operations is all now on one screen.
The overall objective of your facility is to have maximum productivity and a cost-effective organization. The other extreme is constantly running in an unorganized fashion with countless mistakes following right behind you.
How to Meet Customers’ Expectations With Proper Dock Management
There are countless ways to improve customer expectations, but with respect to dock management, dock scheduling software applications must include these 4 key measures:
★ Integrate labour management with a dock schedule to avoid over- or under-scheduling.
★ Manage safety by avoiding overworked staff and maintaining a proper equipment roster and maintenance schedule in tandem.
★ Take advantage of cross-docking, reducing carrying costs in the facility, and improving profitability.
★ Let technology by the traffic cops, which as explained by Bridget McCrea of Modern Materials Handling, integrate with your systems and provide the resource for powering data analytics.
Put the Power of Dock Scheduling Systems to Work Now
The right dock scheduling systems make or break the efficiency of your warehouse, your replenishment practices, your carrier relationships, and customer service levels. Stop hemorrhaging money with outdated dock practices; and, request a demo online of the C3 Solutions dock scheduling platform today.