What We Can Learn From F1 Logistics
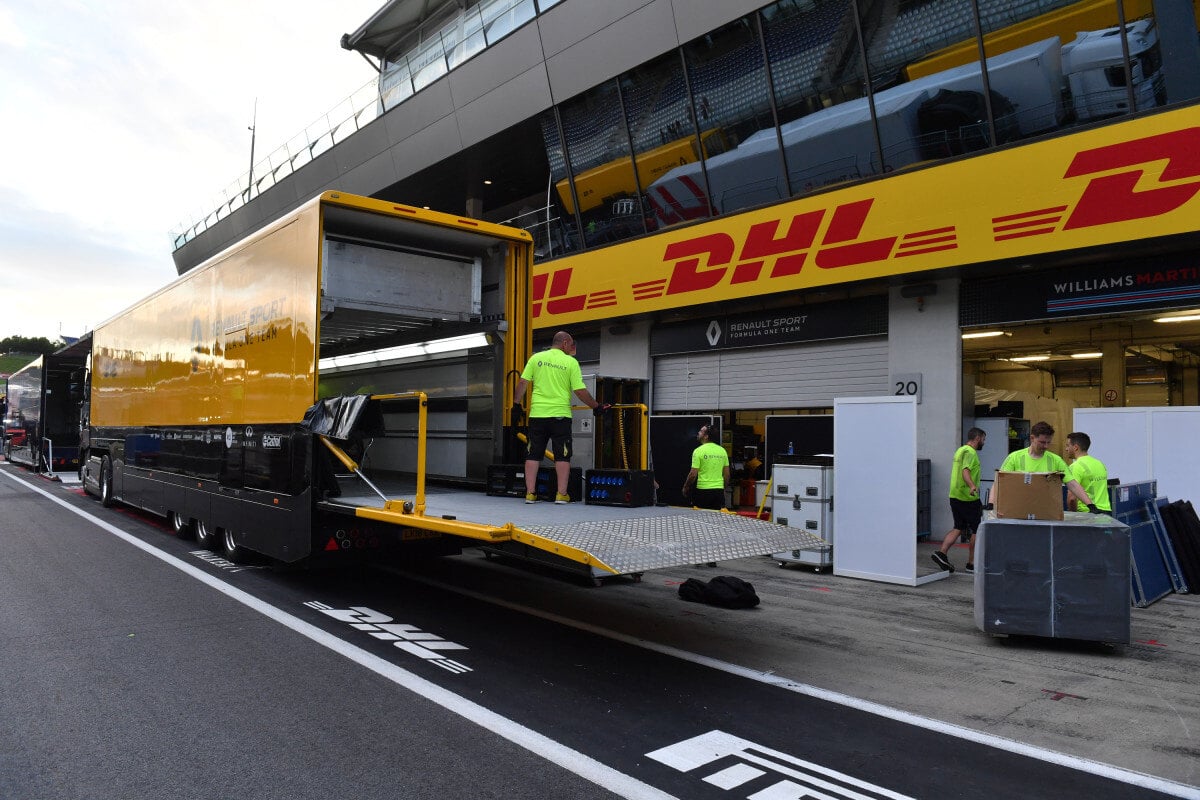
The Grand Prix of Montreal took place recently in our hometown. We had a chance to tag along for a behind-the-scenes logistics tour with DHL, which has the principal logistics contract for Formula 1 around the world.
The scope and complexity of this operation is awe-inspiring, especially when you consider the accelerated timelines and zero tolerance for error that the professional racing series requires. DHL has 20 years of experience moving the F1 and just signed a new contract for another nine years.
With a 24-race season in 2024 for the first time, DHL is responsible for moving all 10 teams and their equipment around the world, multiple times. Coming to Montreal, the teams had just completed the Monaco Grand Prix, so they had to pack up their cars and equipment and return to their European home bases, quickly re-pack and deliver their equipment to DHL depots in Europe. From there, the critical equipment and cars were air freighted by DHL to Canada. The majority of that gear arrived on site in Montreal a few days before the event so that teams had time to assemble the cars and work out any issues.
Additional equipment, that DHL calls “late freight” trickles in right up to the start of racing on the Saturday, and is typically shipped on commercial flights. As we walked in the pit area for GP du Montreal numerous crates of late freight were being delivered and dropped off at teams’ garages.
Many moving parts
Meanwhile, other equipment that was used for the Miami GP a few weeks earlier, was shipped in 100 trucks through the Eastern US to Montreal. The teams have multiple sets of some gear; one is left in North America another stays in Europe, while yet more is allocated to Asia. DHL stores much of this equipment between events because shipping it is too costly and time consuming.
“Every team has like four or five or six kits and it's always moving even off season. We ship the cargo for the first race of the next season,” said Mathieu Levasseur, Motorsports Event Manager at DHL Global Forwarding during the Montreal tour.
He explained that some gear was shipped by ocean after the Japan race in early April, for arrival in early June in Montral. “Ocean freight, they always plan ahead like a good month and a half before.”
And the logistics challenge doesn’t end when the race begins. As soon as that checkered flag is waved teams have seven hours to get packed and ready for DHL to pick up their crates. “Because I'm a logistics geek, I would prefer almost watching the teams packing, which is a race after the race. It's ridiculous how fast they operate just to repack it. Everybody knows which part goes in which kit,” Levasseur said.
A real bottleneck
The Circuit Gilles Villeneuve where the Montreal F1 is particularly challenging from a logistics perspective because there are just two access roads to and from the small island (Ile Notre-Dame) where the race takes place.
Talk about a bottleneck!
When you consider the number of DHL trucks that need access, along with all the workers, food, swag and so on that has to get into the park during the week before the event. Plus, there are multiple support races that also need access to the island. And, the brides are narrow, so that when a transport truck needs to cross, other traffic must be held to let it pass.
So much planning goes into making an event like this work. There really is no leeway for error, and all the parts must act together like clockwork.
Intelligent planning
The DHL organizers wouldn’t reveal their secrets for managing all that inbound and outbound freight, except Levassseur said there was no artificial intelligence (AI) in use, he is the real intelligence behind the planning.
But imagine in your own operation if you had to manage such tight timelines and huge volume on a regular basis. It would be a no-brainer to adopt an automated scheduling system like C3 Reservations for your docks.
Instead of planning and managing on a spreadsheet or paper, all your inbound and outbound trucking companies can make their own reservation at a time convenient to them, that also works for you. Changes are also managed by the software, so you don’t need dedicated people to make the calls or send the emails to confirm and change appointments.
C3 Reservations can also help organize and prioritize loads, so when you have something time critical – like a piece of a racecar coming in hours before the race start – you can automatically manage those priorities. The system is as versatile as the variety of businesses that already use our automation.
So whether your business is time crunched and hectic like the Formula 1, high volume, or just taking too much precious time and energy to coordinate at the docks, we can help. Give us a call to find out more.