What are the Challenges of Dock Scheduling in Grocery Supply Chains?
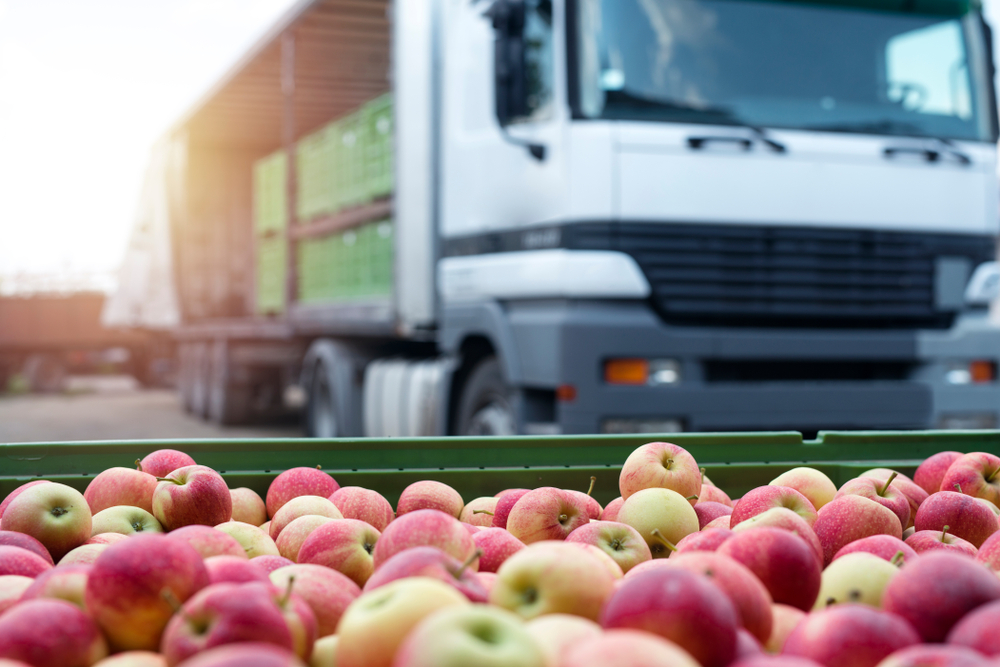
High-quality dock scheduling is crucial to grocery supply chains. The right dock schedule will speed up replenishment and avoid delays in unloading. Unfortunately, the rising complexity and variety of suppliers as well as changing trucking regulations lead to problems with maintaining a quality dock schedule. Supply chain executives and professionals in the food industry need to understand the challenges of dock scheduling in grocery supply chains and here are a few tips to overcome some of these challenges.
Drivers Are Unwilling to Sacrifice Hours for Inconsistent Retailer Docks
As explained by Russell Redman via Supermarket News, retailers and wholesalers cited problems with truckers as a critical issue in managing dock scheduling among grocery supply chains. Specifically, the electronic logging devices (ELD) mandate effectively eliminated the wiggle room truckers had historically for adjusting to meet the demands of each dock. As a result, the following issues have emerged:
1. HOS regulations require drivers to count time in detention as driving hours. Unfortunately, this leads to drivers with less time making money, resulting in the assessment of detention fees. However, such detention fees are only a fraction of what drivers may make while driving.
2. HOS regulations limit drivers to 11 hours, including a 1-hour break. Even though a driver is sitting within detention time, existing HOS regulations mandate such time is counted as driving time further restraining drivers' ability to make money and adversely impacting grocers' profitability as well.
Multiple Systems Exist to Streamline Supply Chain Processes, Leading to Integration/Compatibility Problems
As supply chains have evolved, numerous systems, including homegrown platforms, have been developed to fulfill every possible need, especially in terms of cost control, notes Material Handling & Logistics. Unfortunately, the variety of systems in use today, including WMS, YMS, TMS, WES, WCS and many more, require information to function, and errors in manual data entry may exist. Even though an error may occur harmlessly, the resulting impact on dock scheduling for grocery supply chains can be profound, explains Steve Banker of Forbes. The proliferation of supply chain platforms, as well as the proliferation of volume and variety of vendors, are contributing to higher dock activity. While the obvious solution is to reduce the frequency of deliveries, this is not possible and would have a resounding effect on consumers. So, grocery supply chains need an alternative, such as freight consolidation.
Consolidation Leads to Lost Time De-consolidating Freight During Unloading
Although freight consolidation offers the promise of reducing dock activity and optimized processes, receiving consolidated freight will lead to lost time de-consolidating freight during unloading. Instead of trying to deconsolidate freight on the dock, shippers should consider moving freight indoors and deconsolidating within the warehouse or facility. Of course, this could have additional implications for disruption of customer experiences, so more shippers have developed a preference for receiving product off-hours. Unfortunately, receiving product during off hours will effectively limit the time for carriers to deliver freight, contributing to additional capacity issues.
Leverage a Dock Scheduling System to Overcome These Issues
The right dock scheduling solution will empower grocers with better planning, communication and risk management in managing inbound freight. Unfortunately, the challenges of dock scheduling in grocery supply chains will only grow in complexity, so the key is to develop a plan for addressing all potential challenges. In other words, it is time to transform dock scheduling from a manual, labor-intensive process through dock scheduling software. Learn more about the benefits of dock scheduling software for your business by requesting a demo at C3 Solutions online or calling 1-514-315-3139.