Improving Truck Turnaround Times - How do you Deal with It?
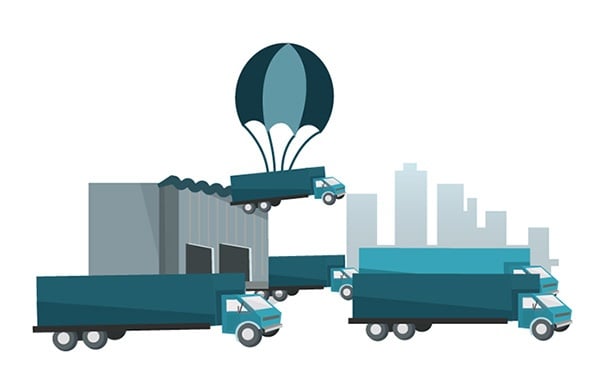
If you catch your site manager saying ‘’Trucks simply show up and we deal with it’’, then it may be time to do a serious analysis of your dock operations.
While this approach is common in many warehouse and distribution environments, relying on reactive measures often results in inefficiencies that lead to higher costs and operational bottlenecks.
This blog dives into the challenges of managing truck arrivals and how structured processes can significantly reduce truck turnaround times, ultimately boosting warehouse efficiency.
The Impact of Truck Turnaround Times on Warehouse Operations
Truck turnaround time (TTT) is a critical metric in logistics. It refers to the total time a truck spends on site—from the moment it arrives at the gate to its departure after loading or unloading. Delays in this process can lead to increased transportation costs, carrier chargebacks, and lower customer satisfaction. According to a 2023 study by Logistics Management Magazine, nearly 60% of logistics managers reported that reducing truck turnaround times was a top priority for their operations.
Having worked in various warehouse environments, I know firsthand the pressure of dealing with these challenges. While the adrenaline rush of managing logistics in a high-pressure setting can be satisfying, it's essential to recognize when reactive management is causing more harm than good. Optimizing your dock operations not only reduces stress but also has significant financial and operational benefits.
Understanding Truck Volumes: Categorizing the Challenges
To understand the best approach for your site, it’s important to categorize truck volumes and their respective impacts on operations:
-
Low Volumes of Trailers (1-10 per day)
In facilities with low volumes, trucks typically experience minimal delays. Since arrivals are spread out, drivers seldom face long wait times. However, the focus should still be on maintaining efficiency and ensuring that these trucks are processed promptly to maximize resources.
-
High Volumes of Trailers (40+ per day)
Warehouses handling high volumes of trailers often implement an appointment scheduling system. These systems manage live loads effectively, reduce congestion risks, and prioritize loading/unloading tasks. For instance, Walmart reported a 30% improvement in truck turnaround times across their distribution centers in 2022 after implementing a dock scheduling system. For high-volume sites, having structured processes in place is not optional—it’s essential.
-
Intermediate Volumes (10-40 Trailers per Day)
This category is the most challenging to manage. Many sites handling intermediate volumes opt to “deal with it” without implementing a scheduling system, reacting only when congestion occurs. This approach often results in inconsistent truck turnaround times and affects warehouse productivity.
The Hidden Costs of ‘Dealing with It’
Facilities in the intermediate volume category that choose a reactive approach often overlook the cumulative costs associated with this decision. Let’s break down some of these costs:
-
Excessive Driver Wait Times
Waiting time is one of the most critical issues. According to the American Transportation Research Institute (ATRI), detention times (delays over two hours) can cost up to $1.1 billion annually in the U.S. alone. Extended wait times affect drivers’ schedules, lead to chargebacks from carriers, and can even influence a site’s reputation, resulting in higher transportation rates. For instance, a 2021 report by Transport Topics noted that 70% of trucking companies factored in wait time risks when setting transportation rates for warehouses with a history of delays.
-
Disrupted Warehouse Productivity
Pulling warehouse staff from regular tasks like picking and put-away to handle unexpected truck arrivals disrupts workflow. A McKinsey study highlighted that inefficient scheduling could reduce warehouse productivity by up to 15%. In an environment where every minute counts, this type of disruption significantly impacts overall efficiency and profitability.
-
Increased Labor Costs
Unscheduled and unpredictable truck arrivals often necessitate overtime pay for dock workers, particularly when volumes peak at the end of a shift. For example, a California distribution center reported an increase of 12% in overtime pay in 2023 due to unplanned trailer arrivals, leading to over $100,000 in additional labor costs annually. Conversely, when operations are slow, dock workers may remain idle, representing a hidden cost that further erodes profitability.
-
Challenges with Resource Planning
Resource planning is critical in managing dock operations effectively. Floor-loaded trailers require significant manpower to unload, and receiving multiple such loads simultaneously can throw off planning. A Grocery Distribution Network in Texas found that without a structured dock scheduling system, they faced a 20% increase in offloading times, leading to additional costs and strain on warehouse staff.
-
Employee Stress and Morale
It’s not just about costs—employee well-being plays a crucial role. Reacting to unpredictable truck arrivals creates unnecessary stress for team members and managers. DHL’s 2022 Employee Satisfaction Survey revealed that stress related to unexpected logistics challenges was one of the top three factors affecting warehouse worker retention. High turnover rates further contribute to operational inefficiencies and additional recruitment costs.
Implementing a Dock Scheduling System: The ROI Advantage
If your facility's costs associated with driver wait times, disruptions, and labor exceed a few hundred dollars per month, investing in a dock scheduling system can provide immediate ROI. Here’s how:
-
Reduced Wait Times and Increased Efficiency
Optimized scheduling allows for better planning, reducing wait times. For example, Coca-Cola’s implementation of a dock scheduling system in 2022 led to a 40% decrease in truck turnaround times, saving them approximately $500,000 annually in detention fees and overtime costs.
-
Visibility and Real KPIs
Modern dock scheduling systems provide real-time visibility into dock activity. This visibility allows managers to track key performance indicators (KPIs) like truck turnaround times, peak periods, and resource allocation. A Retail Industry Report from 2023 indicated that facilities with dock scheduling software saw a 50% improvement in KPI tracking accuracy, which in turn led to better decision-making.
-
Enhanced Resource Allocation
Knowing when and how many trucks are expected allows managers to plan labor needs in advance. For instance, a distribution center for a major European grocery chain found that after implementing a scheduling system, they reduced overtime by 30% and achieved more balanced workloads, ultimately improving employee satisfaction by 20%.
Overcoming Common Objections to Dock Scheduling Systems
Despite the clear benefits, some managers may resist implementing a scheduling system due to concerns about costs or complexity. Here are a few common objections and how to address them:
-
"It’s too expensive."
While there are upfront costs associated with implementing a scheduling system, the ROI often covers these within months. A 2023 survey by Inbound Logistics found that 75% of facilities saw a return on investment in under six months, primarily through reduced wait times and optimized labor costs.
-
"It’s too complicated for our operations."
Modern dock scheduling systems are designed to be user-friendly and adaptable. C3 Solutions, for example, offers solutions specifically tailored for small to medium-sized operations, providing a simplified interface that requires minimal training while delivering maximum impact.
-
"We’ve managed without it so far."
This objection often comes from a place of comfort with the status quo. However, as volumes grow and supply chain complexity increases, relying on manual processes can become a liability. By implementing a system now, facilities can future-proof their operations, ensuring they are well-positioned to handle increased volumes and maintain efficiency.
Conclusion: Don’t Let Pride Overshadow Efficiency
While taking pride in rising to logistical challenges is admirable, it’s crucial not to let pride get in the way of operational efficiency. Leveraging affordable technology can transform your dock operations, reducing truck turnaround times, and improving warehouse performance.
Consider the numbers: if each truck delay costs an average of $50 and you have 15 delays per day, that’s over $20,000 annually—costs that could be avoided with a scheduling system. Instead of “dealing with it,” facilities can adopt a proactive approach that not only saves money but also enhances productivity, employee satisfaction, and overall site performance.
Are you ready to take the next step in improving your truck turnaround times and optimizing your warehouse operations? Contact us for a demo of our dock scheduling system and see how you can start saving time and money immediately.