L'effort sans papier : Comment s'adapter à la nouvelle normalité
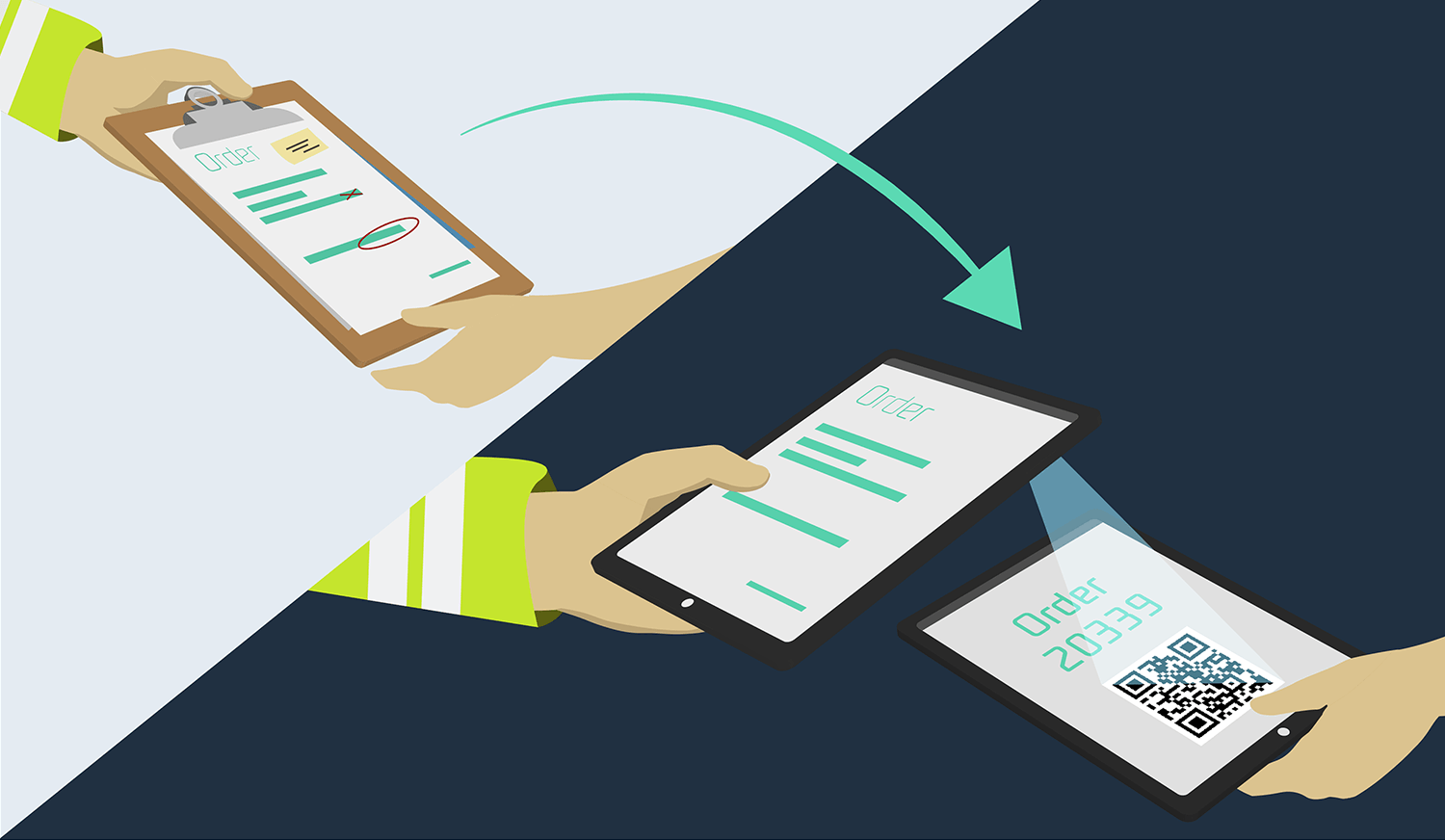
15 min Read |
Do you remember when paperless efforts in the supply chain were only related to 'green' initiatives? Saving paper was the big thing - and still should be; but, this pandemic has driven a renewed demand for avoiding paper.
Content
As explained to us recently by a grocery customer of ours, the contamination risk occurs every time papers exchange hands. According to them, the shipment related paperwork exchanges hands at least six times within a short period of time; including when the driver arrives at the gate (guard verifies paperwork), then at the receiving office (second verification) and when the papers are transferred to the receiving staff in the warehouse and then back to the driver who must interact another time with the gate guard before leaving.
Are we exaggerating or panicking? After some brief searches we quickly came to understand that the risk of transmitting viruses via paperwork is relatively low. Droplets generated by coughing are most potent (via airborne infection), followed by the contact of hands and then other surfaces (ie. paper).
So why are our clients so concerned about this? It appears to us that the companies we’ve spoken to so far wish to spare no effort to reassure employees that they are safe and protected in their work environment.
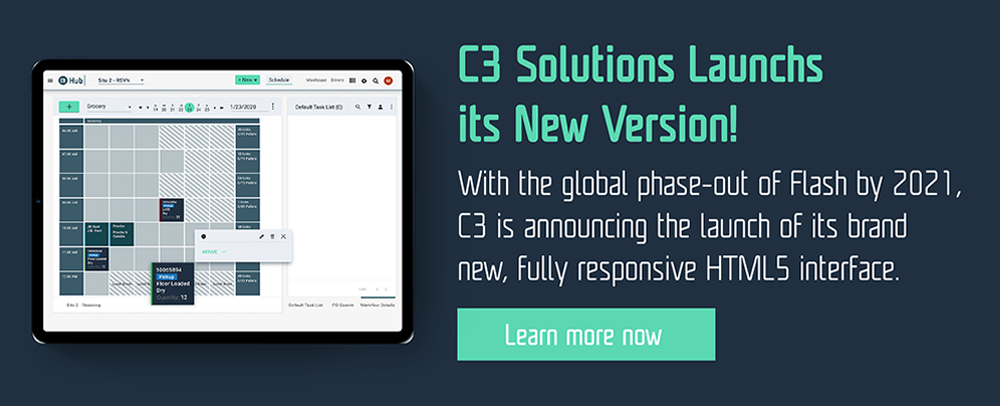
The Future is Paperless
Many are aware that Adobe software is stopping support for Flash at the end of 2020, forcing those who were using Flash to upgrade their software platforms to the fifth generation of HTML.
C3 is among those companies that has started upgrading their customers to HTML5. This means that software like ours have become 100% mobile friendly; eliminating the need to download apps from the app stores. This facilitates the collaboration among all users since our progressive web applications (PWA) are readily available on any mobile device. Users will be able to consult, on their mobile devices, statuses and file attachments (shipment documents), trigger and approve specific actions based on their access rights, further reducing the need to exchange paperwork.
Recent Case Studies
The following are excerpts of initiatives we’ve recently realized, and that we hope will inspire even more creative ideas. It goes without saying, as proponents of providing advanced notifications to shippers in some form of appointment scheduling, most of these examples gravitate around how an appointment scheduling software can be leveraged in order to reduce the use of paperwork and maintain social distancing.
Helping Grocers Stay Safe
We start with an obvious one, that is to upload all shipment paperwork as a file attachment to the appointment request. Even though appointment scheduling might not be a requirement in your business, it does serve the purpose of providing a pre-arrival notification; through which all the paperwork can be attached. Attaching documents online with the appointment request isn’t new; the initial purpose was to ensure that drivers do not forget the paperwork (causing delays at the gate/receiving office). With the current pandemic, customers are discovering an added benefit.
As outlined in the opening paragraphs, our grocery customer now wants to implement mandatory file attachments to the appointments for all shipments. This means the gate guard will be able to consult the documentation online just like all the users throughout their receiving process. Additional documents can be added, fault and audits conducted, maintaining 100% visibility and control online without physically exchanging paperwork.
If drivers are concerned about social distancing when arriving at a site, they can use the appointment confirmation email to display the barcode for easy scanning. If specific instructions need to be provided to the driver, an appropriate printer can be installed outside the gatehouse so that the drivers can access their gate pass details.
A Lesson in Connectivity
There isn’t a software system that can pretend to be a complete end-to-end solution for a paperless supply chain. Therefore connectivity, through various forms and protocols, is essential to promote productivity while ensuring security.
In one such example, an Australian retailer asked us to collaborate with them in adapting our scheduling software (called time slotting, Down Under) to their automated gate initiative. They already had advanced C3 Hub configuration features such as driver validation, and are taking full advantage of the external portal for suppliers and carriers to book their appointments. Chain of Responsibility (CoR) is law in Australia, so carriers and suppliers are used to collaborating with shippers in providing the necessary information in the appointment details.
Using a third party kiosk hardware and software, the retailer has asked C3 to communicate the appointment data in real-time through web APIs. The drivers will enter their reference number in the kiosk and will receive validation and directions to which door to go to. In this example, the web APIs not only exchange information but also trigger transitions; that is, it can communicate directly to our appointment scheduling software that the driver has arrived, is at door, departed, etc. Although this project was first initiated with the objective of obtaining productivity gains through automation, they now feel their site is more secure from the risk of COVID-19 contamination.
Keeping the Solution Simple
There are technology driven solutions that may seem out of reach for your business at this time. You may be looking for small wins that don’t require a significant investment in capital and project resources.
For example, a retail customer testified that it wasn’t ready to have an automated entry point to their site, for reasons that are out of scope of this article. However, could we maybe help them to make the departure of drivers paperless? Once on site, whether to deliver or pick up, drivers have submitted all the information regarding their tractor and load numbers. The logistics team now has the necessary control and visibility over the asset and driver information. By installing license plate recognition software at the outbound gate (reasonably priced), all the proper verifications (driver, tractor, load, etc.) can be done in advance in the shipping/receiving office and made visible to all via the yard and dock management software. Through simple data integration work, the license plate number is being sent to the license plate recognition software that, once validated, opens the gate barrier to the drivers.
In a final example, a beverage distributor didn’t quite eliminate the paper but was able to simplify the process and protect the shipping team and drivers from propagating the virus. The shipping lead prints at their station a summary of the purchase orders being picked up as per the schedule, and inserts on top of the rest of the paperwork in a clear plastic sleeve. The clear plastic sleeve is cleaned before being handed over the shipper loading the truck. Using C3 Hub on their mobile devices, they are able scan the barcode, visible through the clear plastic, allowing the loading personnel to confirm that the truck is finished loading and ready to depart without manipulating the paperwork directly. The plastic sleeve is then safely handed over to the driver while respecting social distancing protocol.
In the End...
We’ve all witnessed wonderfully creative solutions showing how people are adapting to the COVID-19 pandemic. We recognize that these are modest in scope but we are hopeful they may stimulate even more creative ideas, and contribute in making our respective work environments safer and more efficient.
As always you can comment on this article, share your ideas with us, or contact us directly for more information about our scheduling and yard management software solution.