Using the 5 S to Analyze your Dock Operations
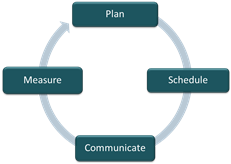
I recently met with a logistics consultant with whom I discussed specific mandates where lean logistics (reducing costs while improving performance) was successfully implemented in warehouse and store operations. It prompted me to learn more about lean logistics, 5 S’s and continuous improvement practices and examine how this relates to the challenges involved with dock scheduling. Here are some examples of these challenges and how they relate to the 5 S’s.
Seiri (Sorting)
It’s all about eliminating unnecessary tools which clutter your receiving/shipping office. Too many warehouses still use the paper calendars, whiteboards, multiple spreadsheets or shared calendars in an attempt to plan and organize their schedule. All these tools clutter the office area because the information is haphazard. These tools also generate an enormous amount of phone calls and emails because of the lack of visibility; thus cluttering voice mails and Inboxes. An online dock scheduling software with portals and automatic email communications solves this.
Seiton (Straightening)
This represents orderliness. Is the appointment information accurate, accessible and retrievable quickly and efficiently? Many accounts I speak with complain that the information provided by the carriers, upon requesting an appointment, is incomplete or inaccurate. In other cases, we often hear about customer service groups regularly phoning the warehouse to learn about the status of a shipment. To cite another account: after they audit the shipment, staple the PO information with the infractions, then the information gets lost in the filing cabinet. All of these elements of disorder can be dramatically improved through the added visibility that a dock appointment scheduling system can provide.
Seiso (Shining)
The word ‘shining’ is convenient for its first letter but this truly stands for cleanliness. The first thing that comes to mind is eliminating paper. Start by eliminating the paper calendars and audit forms. Have carriers and vendors attach electronic versions of the bill of ladings and packing lists to the appointment request. Replace the unruly whiteboard in the warehouse with a screen which lists in real-time the upcoming appointments.
Seiketsu (Standardization)
All organizations with multiple warehouses and stores struggle with the standardization process. With multiple warehouses, the challenge is heightened due to the different square footage and product mix specific to each location. You need a dock scheduling solution which is flexible enough to adapt to each location’s reality and business priorities while respecting the company’s standards and policies.
Shitske (Sustaining)
Sustaining a 5 S initiative requires discipline and rigor. Management often complains that they don’t have the tools to render their carriers and vendors accountable, nor can they truly monitor the scheduling team’s efficiency. This requires real-time dashboards and reporting tools to monitor, diagnose, and enforce their receiving and shipping standards.
Interestingly enough, I also learned that an additional 3 S’s have been added, representing Safety, Security and Satisfaction.
These additional 3 S’s fit extremely well for addressing the auditing and scorecarding initiatives in the warehouses and stores. For example, a retailer currently audits the quality of the load arriving to the stores from the DC, examining whether it was properly loaded (weight distribution and stacking of pallets) for safety and security reasons. In order to measure the overall satisfaction relative to the quality of the shipment, the warehouse captures infractions on the traditional parameters, such as quantities, damages, incorrect paperwork, etc. Again these are all areas that are very manageable with a proper dock scheduling system but next to impossible from a manual perspective.
Considering all this, I hope you’ll agree that dock scheduling is an excellent area to apply the principles of the 5 S’s in lean logistics; providing you a great tool to discover the inefficiencies in your dock operations. For more information about C3 Solutions’ cloud-based dock scheduling and compliance solutions, please request a free demo.