Carrier Late Arrivals – How To Deal With It
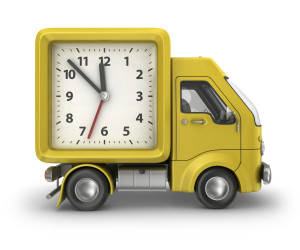
We recently hosted a webinar where two warehouse managers talked about their scheduling operations, before and after implementing C3’s dock scheduling system. One of the questions that was asked from the audience is one that we often discuss with prospective clients.
How does your warehouse manage late arrivals?
I felt it relevant to share with our readers their response and complement the webinar with the feedback we regularly obtain in the market. In summary, the webinar speakers agreed on the following approach to managing late arrivals.
- The need to establish a company policy outlining what is considered a late arrival.
- The webinar speakers’ preferred choice when a carrier arrives late is to work them into the next available slot. This directive is dependent on the priority of load, day of the week (weekday or weekend?), and time of day (end of shift?).
- Disciplinary action, whether they be chargebacks or not, is first and foremost intended to motivate carriers to be on time.
In both cases, their policy dictates a late arrival to be 30 minutes past the appointment time. From our experience, it appears that 20 to 30 minutes is common, with 15 minutes being the most stringent requirement we’ve seen.
If a carrier needs to be unloaded at the end of a shift, one of the speakers charges $90 per hour to compensate for the overtime labour; but emphasizes that this penalty is a minor consequence and that the desired behaviour is that the carrier arrive on time. The other speaker doesn’t apply chargebacks but refuses to retain personnel beyond the end of the shift if the carrier is late. In this case, a carrier may need to stay overnight in order to be unloaded in the morning.
There’s more to consider than simply managing late arrivals.
Unfortunately, simply dealing with late arrivals won’t address all the issues surrounding loads that don’t arrive on time. Situations such as early and very late arrivals as well as ‘no shows’ can easily disrupt your planning.
In the case of early arrivals, the typical warehouse has two options.
- Tell the driver to come back for the confirmed time.
- Enrol the driver on a waiting list (standby) in case an opening is created between now and the appointment time.
At face value, an early arrival doesn’t appear to be a significant issue, but it is disruptive and time consuming for the shipping/receiving clerk. Essentially, it doubles the work as they are forced to greet the driver twice. If it is beneficial to your operation to receive early appointments, you should create a standby list in order to keep track of the waiting drivers.
One of the reasons warehouses allow drivers to ’standby’ is due to the number of ‘very late’ loads that arrive (or in some cases never arrive). As a carrier becomes ‘very late’, the reserved appointment time now becomes available to standby appointments. This allows the warehouse to accommodate early arrivals and minimize lost productivity to excessively late carriers.
For drivers that simply don’t show up, you need to determine what is regarded as ‘no show’ and what are the ramifications to being a ‘no show’. Some companies prefer that carriers then reschedule the load. This may depend on the capabilities of the scheduling system you use and whether you wish to discipline a ‘no show’ or simply track the total number of hours the driver is late.
Reporting
If companies manually track appointments, amendments and arrival times, reporting these events usually requires a labour intensive spreadsheet. Regardless of how it’s managed, proper reporting tools are essential in order to eliminate conflicting positions regarding late arrivals. Your company policy regarding late arrivals may be limited by your reporting capability; be aware that you can’t enforce a stance that you can’t prove.
Conclusion
The timeliness of the shipment is of utmost importance to your warehouse operations. Reality and human nature means that late arrivals do occur and warehouses need to find an equilibrium by managing these situations reasonably while making carriers accountable.
If you wish to hear actual warehouse managers answer this question, please listen to this abbreviated version of the webinar.
The full webinar transcript is also available here.
To find out more on C3 Solutions' dock scheduling system, sign up for a free Web demonstration.